Areas where factories Sugar lose money
- hr30522
- Aug 2, 2024
- 8 min read
Updated: Nov 23, 2024
Sugar factories play a pivotal role in the global economy, providing a crucial ingredient for countless products and industries. Despite their importance, these facilities often face significant financial challenges that can impact their profitability. To help understand these issues better, let’s explore in detail the areas where sugar factories might lose money, and discuss strategies to address these challenges.
1. Production Costs and Efficiency:
Production Costs:
Production costs in sugar factories encompass a wide range of expenses, including raw materials, labor, energy, and maintenance. High production costs can significantly reduce profit margins, especially if they are not managed effectively. Factors such as outdated technology, inefficient processes, and high waisted levels contribute to increased production costs.
Efficiency Challenges:
Operational inefficiencies can stem from various sources: poorly designed workflows, inadequate staff training, or outdated machinery. For instance, factories using older equipment might experience higher breakdown rates and increased maintenance costs, leading to production delays and added expenses.
Process Optimization:
Implementing lean manufacturing principles can help streamline operations, reduce waste, and enhance efficiency. Techniques such as Six Sigma or Kaizen can be useful for identifying and eliminating inefficiencies.
Technological Upgrades:
Investing in modern machinery and automation can lead to significant cost savings by improving production speed, precision, and overall efficiency.
Regular Training:
Providing ongoing training for employees ensures they are up-to-date with the latest best practices and technologies, leading to improved productivity and reduced errors.
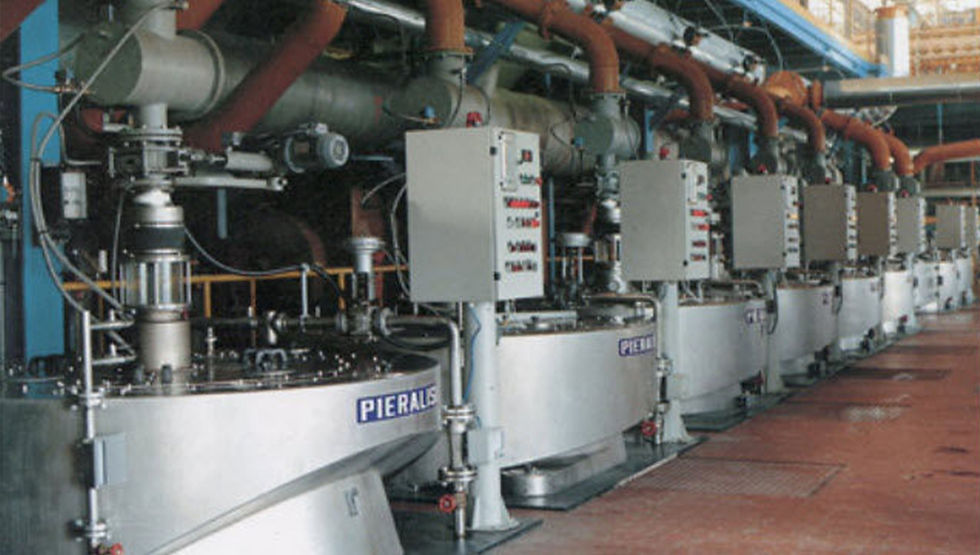
2. Raw Material Prices:
Fluctuating Raw Material Costs:
The cost of raw materials, particularly sugarcane, can fluctuate due to various factors such as weather conditions, global market trends, and geopolitical issues. These price variations can significantly impact a factory’s financial stability. For example, a severe drought could lead to a shortage of sugarcane, driving up prices and increasing production costs.
Impact of Price Volatility:
Volatility in raw material prices can make budgeting and financial planning challenging. Factories may struggle to maintain stable profit margins when raw material costs rise unexpectedly, affecting their overall financial performance.
Long-Term Contracts:
Securing long-term contracts with suppliers can provide more price stability and predictability. Factories can negotiate fixed prices or price caps to mitigate the impact of price fluctuations.
Diversification:
Exploring alternative raw materials or sources can reduce dependency on a single supplier or crop. For instance, using alternative sugar sources like beet sugar or exploring regional suppliers can help manage costs.
Inventory Management:
Maintaining an optimal inventory level can help balance the risks associated with price fluctuations. Factories should use inventory management systems to track raw material usage and forecast future needs.
3. Labor Costs and Productivity:
High Labor Costs:
Labor costs can be a significant expense for sugar factories, encompassing wages, benefits, and overtime. In regions with high labor costs, these expenses can eat into profit margins, especially if productivity levels are not high.
Labor Productivity Issues:
Low labor productivity can stem from various issues, including insufficient training, lack of motivation, or outdated processes. For example, workers using manual methods may be less efficient than those utilizing automated systems, leading to slower production times and higher labor costs.
Training and Development:
Investing in employee training and development programs can enhance skills, increase productivity, and reduce errors. Regular workshops and skill-building sessions can ensure that workers are proficient with the latest technologies and methods.
Incentives and Motivation:
Implementing incentive programs or performance-based rewards can motivate employees to work more efficiently. Recognizing and rewarding high performance can lead to increased job satisfaction and productivity.
Workforce Optimization:
Analyzing labor needs and optimizing workforce allocation can help manage labor costs. For example, scheduling shifts based on production demands can minimize overtime and reduce costs.

4. Energy Consumption:
Energy-Intensive Production:
Sugar production is highly energy-intensive, with significant energy requirements for processes such as boiling, drying, and milling. High energy consumption can lead to elevated operational costs, especially when energy prices are volatile.
Energy Efficiency Improvements:
Implementing energy-efficient technologies, such as high-efficiency boilers, variable-speed drives, and advanced lighting systems, can reduce energy consumption. For example, upgrading to LED lighting can lower electricity usage and costs.
Renewable Energy Sources:
Exploring renewable energy options, such as solar or wind power, can provide long-term cost savings and reduce dependency on traditional energy sources. Investing in renewable energy infrastructure can also enhance a factory’s sustainability efforts.
Energy Audits:
Conducting regular energy audits can help identify areas of excessive energy use and opportunities for improvement. Implementing energy-saving measures based on audit findings can lead to significant cost reductions.
5. Equipment Maintenance and Downtime:
Importance of Equipment Maintenance:
Regular maintenance of equipment is crucial for preventing breakdowns and ensuring smooth production. Unplanned equipment failures can lead to costly repairs, production delays, and operational downtime.
Preventive Maintenance:
Implementing a preventive maintenance program involves scheduling regular inspections and servicing to address potential issues before they lead to breakdowns. For instance, routine checks on machinery components can prevent unexpected failures.
Predictive Maintenance:
Utilizing predictive maintenance technologies, such as sensors and data analytics, can help predict equipment failures based on performance data. This approach allows for timely interventions and reduces the risk of unplanned downtime.
Maintenance Training:
Providing training for maintenance staff ensures they are equipped with the skills and knowledge to perform effective maintenance tasks. Regular training sessions can help keep the team updated on best practices and new technologies.
Impact of Inefficient Waste Management:
Inefficient waste management practices can result in higher disposal fees, regulatory fines, and negative environmental impacts. For example, improper disposal of hazardous waste can lead to legal issues and reputational damage.
Waste Reduction:
Implementing waste reduction strategies, such as process improvements and quality control measures, can minimize the amount of waste generated. For instance, optimizing production processes can reduce defective products and by-products.
Recycling and Reuse:
Exploring opportunities for recycling and reusing waste materials can help lower disposal costs and improve sustainability. For example, reusing bagasse (a by-product of sugarcane processing) for bioenergy or animal feed can add value and reduce waste.
Waste Audits:
Conducting waste audits can help identify areas for improvement and track progress in waste reduction efforts. Implementing changes based on audit findings can lead to more effective waste management and cost savings.
7. Supply Chain and Logistics:
Importance of Supply Chain Management:
A well-managed supply chain is crucial for maintaining production efficiency and controlling costs. Disruptions in the supply chain can lead to production delays, increased costs, and reduced profitability.
Supplier Relationships:
Building strong relationships with reliable suppliers can help ensure timely deliveries and stable prices. Establishing long-term partnerships and maintaining open communication can enhance supply chain reliability.
Inventory Management:
Implementing advanced inventory management systems can help track inventory levels, forecast future needs, and optimize stock levels. For example, just-in-time inventory systems can reduce storage costs and minimize stockouts.
Logistics Planning:
Efficient logistics planning involves optimizing transportation routes, managing shipping costs, and ensuring timely deliveries. Investing in logistics technology, such as route optimization software, can improve efficiency and reduce costs.
8. Quality Control and Product Diversification:
Importance of Quality Control:
Maintaining high product quality is essential for customer satisfaction and market competitiveness. Poor quality control can lead to product recalls, returns, and reputational damage, all of which can impact financial performance.
Robust Quality Systems:
Implementing comprehensive quality control systems can help monitor and ensure product quality at every stage of production. For example, quality checks at critical points in the production process can prevent defects and ensure consistency.
Product Diversification:
Diversifying product offerings can reduce reliance on a single product and mitigate risks associated with quality issues. For instance, introducing new sugar-based products or alternative sweeteners can attract different market segments and improve revenue.

9. Regulatory Compliance and Environmental Standards:
Importance of Regulatory Compliance:
Compliance with regulatory requirements and environmental standards is crucial for avoiding legal issues and fines. Non-compliance can result in costly penalties and damage a factory’s reputation.
Regulatory Updates:
Staying informed about changes in regulations and environmental standards is essential for maintaining compliance. Regularly reviewing regulatory updates and engaging with industry associations can help factories stay current with requirements.
Compliance Programs:
Implementing comprehensive compliance programs, including training and audits, can ensure adherence to regulatory requirements. For example, establishing a dedicated compliance team can help manage and monitor regulatory obligations.
Environmental Initiatives:
Investing in environmentally friendly technologies and practices can help meet regulatory standards and enhance sustainability. For instance, implementing waste reduction and energy efficiency measures can contribute to regulatory compliance and improve environmental performance.
10. Financial Management and Cost Control:
Importance of Financial Management:
Effective financial management is critical for maintaining profitability and ensuring long-term financial stability. Poor financial management can lead to overspending, inadequate budgeting, and financial strain.
Cost Control Measures:
Implementing cost control measures involves monitoring and managing expenses to stay within budget. For example, conducting regular financial reviews and setting budget limits can help control costs.
Financial Analysis:
Regularly analyzing financial performance can provide insights into areas for improvement and help identify cost-saving opportunities. For instance, analyzing financial statements and key performance indicators can guide decision-making and improve profitability.
Budgeting and Forecasting:
Developing accurate budgets and financial forecasts can help manage resources and plan for future needs. For example, creating detailed budgets for different departments and forecasting future revenue and expenses can enhance financial planning.
11. Market Prices and Economic Fluctuations:
Impact of Market Prices:
Market prices for sugar and related products can fluctuate due to economic conditions, trade policies, and global demand. These fluctuations can impact a factory’s revenue and profitability.
Hedging Strategies:
Utilizing hedging strategies can help manage price volatility and protect against adverse price movements. For instance, entering into futures contracts can lock in prices and reduce the impact of price fluctuations.
Market Research:
Staying informed about market trends and economic conditions can help factories make informed pricing and production decisions. Regular market research and analysis can provide insights into demand patterns and price trends.
Flexible Pricing:
Implementing flexible pricing strategies can help adjust to changing market conditions. For example, using dynamic pricing models that respond to market fluctuations can help optimize revenue and maintain competitiveness.
12. Innovation and Technological Advancements:
Importance of Innovation:
Innovation is crucial for maintaining competitiveness and improving financial performance. Embracing new technologies and processes can lead to more efficient production, better quality control, and reduced costs.
Research and Development (R&D):
Investing in R&D can lead to the development of new products, processes, and technologies. For instance, exploring new sugar extraction methods or alternative sweeteners can enhance product offerings and improve efficiency.
Technology Adoption:
Staying updated with technological advancements and adopting relevant technologies can improve production processes and reduce costs. For example, implementing advanced data analytics or automation systems can enhance operational efficiency.
Collaboration and Partnerships:
Collaborating with research institutions, technology providers, and industry partners can drive innovation and provide access to new technologies and insights.

13. Debt Management and Financial Stability:
Impact of High Debt Levels:
High debt levels can result in higher interest expenses, reduced financial flexibility, and increased financial risk. For example, excessive debt can limit a factory’s ability to invest in growth opportunities or respond to economic challenges.
Debt Reduction:
Implementing strategies to reduce debt, such as paying down high-interest loans or refinancing debt, can improve financial stability. For instance, consolidating debt or negotiating better terms with creditors can help manage debt levels.
Financial Planning:
Developing a comprehensive financial plan can help manage debt and ensure long-term stability. For example, creating a debt repayment schedule and monitoring cash flow can support effective debt management.
Alternative Financing:
Exploring alternative financing options, such as equity investment or asset-based lending, can provide additional capital and reduce reliance on debt. For example, seeking investment from venture capital or private equity can support growth and financial stability.
Conclusion:
Sugar factories face a multitude of financial challenges that can impact their profitability and sustainability. From high production costs and fluctuating raw material prices to labor costs, energy consumption, and regulatory compliance, addressing these issues is crucial for maintaining financial health.
By focusing on efficiency, optimizing processes, investing in technology, and managing financial risks, sugar factories can navigate these challenges and improve their financial performance. Understanding the key areas where sugar factories might lose money and implementing effective strategies to address these issues can lead to more sustainable operations and better financial outcomes.
As the sugar industry continues to evolve, staying informed and proactive will be essential for achieving long-term success and profitability. Embracing innovation, optimizing operations, and managing financial risks will help sugar factories thrive in a competitive and ever-changing market.
Kommentare