Energy Efficiency Trends in Sugar Mill Operations
- hr30522
- Apr 19
- 7 min read
The global sugar industry is undergoing significant transformations, with a heightened focus on improving energy efficiency within sugar mills. As the demand for sugar continues to rise while environmental concerns grow, sugar mill operators face increasing pressure to reduce energy consumption and enhance sustainability. Energy-efficient practices not only help in reducing operating costs but also contribute to a greener and more environmentally responsible sugar production process.
In this blog, we will explore the latest energy-efficient practices and technologies in sugar mill operations. By understanding these trends, sugar mill owners and operators can stay ahead of the curve, reduce costs, and minimize their environmental footprint.
Energy Efficiency in Sugar Production: Why It Matters
Sugar production is an energy-intensive process, primarily relying on electricity and thermal energy sources like steam. The mills utilize large amounts of power for crushing, boiling, drying, and refining sugarcane or sugar beet. As energy costs continue to rise, optimizing energy use in these operations becomes crucial for profitability and competitiveness.
Moreover, the sugar industry contributes to greenhouse gas (GHG) emissions, primarily due to its energy consumption. By implementing energy-efficient technologies, sugar mills can significantly reduce their carbon footprint. Additionally, energy efficiency aligns with global sustainability goals and regulatory pressures aimed at curbing industrial emissions.

Energy Efficiency Trends in Sugar Mill Operations:
In recent years, sugar mills have embraced various energy-efficient technologies and practices, helping them minimize energy waste and increase overall efficiency. These practices not only reduce costs but also enable mills to improve their sustainability credentials. Some of the key trends in energy efficiency within sugar mill operations are:
Cogeneration and Combined Heat and Power (CHP) Systems:
Cogeneration, or Combined Heat and Power (CHP), has become one of the most promising energy-efficient technologies in sugar mills. In a typical sugar mill, steam is generated during the process of extracting juice from sugarcane or beet. Cogeneration systems allow mills to simultaneously produce electricity and utilize the heat for other processes such as boiling or drying. This leads to improved energy efficiency by reducing the need for external energy sources.
The integration of cogeneration in sugar mills enables operators to not only fulfill their internal energy needs but also generate surplus electricity, which can be sold back to the grid. This practice is particularly beneficial in regions where energy supply is inconsistent or expensive. By utilizing both heat and electricity generated during sugar production, mills can significantly reduce their energy consumption and costs.
Key Benefits:
Reduction in overall energy consumption
Ability to sell excess electricity, generating additional revenue
Reduced dependency on external energy sources, increasing energy security
Lower carbon footprint due to more efficient energy use
Energy Management Systems (EMS):
The adoption of advanced energy management systems (EMS) has been another major trend in sugar mill operations. EMS involves the use of software, sensors, and data analytics to monitor and optimize energy consumption in real time. By collecting data on energy usage across various processes in the mill, operators can identify areas where energy is being wasted and take corrective actions.
Energy management systems can help optimize the operation of machinery, adjust lighting and HVAC systems, and ensure that equipment is running at peak efficiency. This level of monitoring and control allows sugar mills to make data-driven decisions that lead to reduced energy consumption and increased operational efficiency.
Key Benefits:
Improved control over energy consumption
Identification of inefficiencies and areas for improvement
Cost savings from reduced energy waste
Real-time insights that enable immediate corrective actions

Use of Energy-Efficient Motors and Drives:
Motors are one of the largest energy consumers in sugar mills, especially in processes such as crushing, pumping, and conveyor operations. Traditional motors often operate inefficiently, consuming more power than necessary and leading to increased energy costs. One of the most effective ways to improve energy efficiency is by switching to energy-efficient motors and variable speed drives (VSDs).
Energy-efficient motors, such as those rated with the IE3 (Premium Efficiency) classification, consume less power while delivering the same level of performance. Additionally, variable speed drives (VSDs) allow motors to operate at optimal speeds based on demand, rather than running at full capacity all the time. This further reduces unnecessary energy consumption.
Key Benefits:
Reduced electricity consumption
Prolonged equipment lifespan due to less wear and tear
Lower maintenance costs and fewer breakdowns
Enhanced process control with VSDs
Heat Recovery and Waste Heat Utilization:
The sugar industry generates significant amounts of waste heat during various stages of production, especially during the boiling and evaporation processes. Traditionally, much of this waste heat is released into the environment, contributing to energy loss. However, modern sugar mills are increasingly adopting heat recovery technologies to capture and repurpose waste heat for other processes.
One of the most common methods of waste heat recovery is through the installation of heat exchangers. These systems capture excess heat from exhaust gases or hot water and transfer it to other parts of the mill where it can be used to preheat water, steam, or air. In some cases, waste heat can be used to generate additional electricity or power industrial processes like drying and cooking.
Key Benefits:
Reduced energy demand for heating processes
Lower fuel consumption and costs
Minimization of environmental impact by reducing waste heat
Improved overall mill efficiency.
Automation and Process Optimization:
The implementation of automation and control systems is transforming energy efficiency in sugar mills. By incorporating advanced process control systems and predictive maintenance, sugar mills can optimize their operations for maximum energy savings. Automated systems help to fine-tune process parameters, ensuring that each part of the production cycle runs as efficiently as possible.
For instance, automation systems can regulate the temperature, pressure, and flow rates during juice extraction, boiling, and crystallization. These systems can automatically adjust the operations to ensure energy is used in the most efficient manner, reducing waste and improving throughput.
Key Benefits:
Greater operational consistency and reliability
Reduced human error and inefficiencies
Improved maintenance scheduling, preventing breakdowns
Enhanced process optimization for better energy utilization

Solar Energy Integration:
In recent years, sugar mills have increasingly turned to renewable energy sources, such as solar energy, to meet their power needs. Solar panels can be installed on the roofs of sugar mills or in nearby areas to generate electricity, which can then be used to power operations. This is especially beneficial in regions with abundant sunlight.
By integrating solar energy, sugar mills can reduce their reliance on grid electricity, lowering costs and contributing to environmental sustainability. Some sugar mills even use solar power to supplement the electricity generated through cogeneration, creating a hybrid renewable energy system.
Key Benefits:
Reduction in electricity costs and carbon emissions
Use of renewable energy contributes to sustainability goals
Improved energy independence and security
Potential for government incentives or subsidies for renewable energy
Biogas Production from Organic Waste:
Sugar mills generate large quantities of organic waste, including bagasse (the fibrous byproduct of sugarcane) and molasses. Traditionally, these byproducts are either burned as fuel or discarded, but new trends are focusing on converting this waste into biogas.
Biogas is produced by the anaerobic digestion of organic materials, and it can be used to generate electricity or heat. This not only reduces the reliance on fossil fuels but also helps sugar mills manage waste more sustainably. The energy produced from biogas can be used internally, and any surplus can be sold to the grid.
Key Benefits:
Reduced waste disposal costs
Renewable energy production from byproducts
Lower greenhouse gas emissions
Contribution to circular economy practices
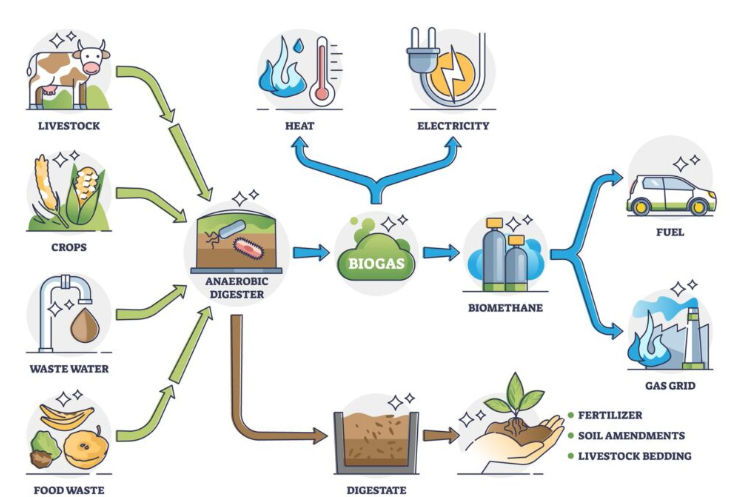
The Future of Energy Efficiency in Sugar Mills:
As global energy costs continue to rise and sustainability regulations become stricter, the sugar industry will undoubtedly place even more emphasis on energy-efficient practices. The future of energy efficiency in sugar mill operations lies in the continued development and integration of advanced technologies.
Artificial intelligence (AI) and machine learning could play key roles in optimizing energy use, predicting maintenance needs, and improving process efficiency. Additionally, the growing trend of sustainability in manufacturing suggests that energy efficiency will not only be a financial imperative but also a social and environmental responsibility for sugar mills.
As energy costs continue to rise and environmental regulations become more stringent, the push for energy-efficient practices in sugar mills will only intensify. The future of energy efficiency in sugar production will likely see the integration of even more advanced technologies, such as artificial intelligence (AI) and machine learning, to further optimize energy usage.
These technologies can help predict energy demand, schedule maintenance, and optimize production processes in real-time, providing even greater opportunities for energy savings.
In addition, the trend toward renewable energy integration will likely continue, with sugar mills exploring other forms of renewable energy such as wind and hydropower. As the demand for sustainable products grows, sugar mills that embrace energy efficiency will not only improve their bottom line but also strengthen their position in a market increasingly focused on sustainability.

Conclusion:
The integration of energy-efficient technologies and practices in sugar mill operations has become a critical factor for success in the modern sugar industry. From cogeneration and heat recovery to automation and biogas production, there are numerous ways in which sugar mills can reduce energy consumption, lower costs, and reduce their environmental impact. These trends represent a significant shift toward more sustainable and cost-effective production processes that will help sugar mills thrive in an increasingly competitive and environmentally-conscious world.
By staying informed about these emerging energy efficiency trends and embracing new technologies, sugar mills can position themselves as leaders in sustainability, contributing to both their bottom line and the broader environmental goals of the industry.
By embracing these trends, sugar mills can not only improve their financial performance but also contribute to a more sustainable future for the industry. As energy efficiency technologies continue to evolve, sugar mills that stay ahead of the curve will be better positioned to thrive in a rapidly changing global marketplace.
Kommentare