Enhancing Sugar Mill Efficiency Through Integrated Automation
- hr30522
- 6 days ago
- 8 min read
The global sugar industry is in constant flux, responding to changes in market demands, operational costs, and environmental challenges. For sugar mills, staying competitive requires not just maintaining current production levels but continually improving efficiency, reducing waste, and enhancing overall productivity. This is where integrated automation plays a pivotal role. Automation in sugar mills is not just a trend; it’s a necessity for staying ahead in a world where operational excellence is key.
Integrated automation systems combine various technologies such as sensors, control systems, software, and machines to create a cohesive, efficient production environment.
These systems help streamline processes, reduce human error, improve energy usage, and ensure the consistency of the end product. In this blog, we’ll explore in-depth how integrated automation can transform sugar mill operations, improve productivity, and contribute to a sustainable future for the sugar industry.
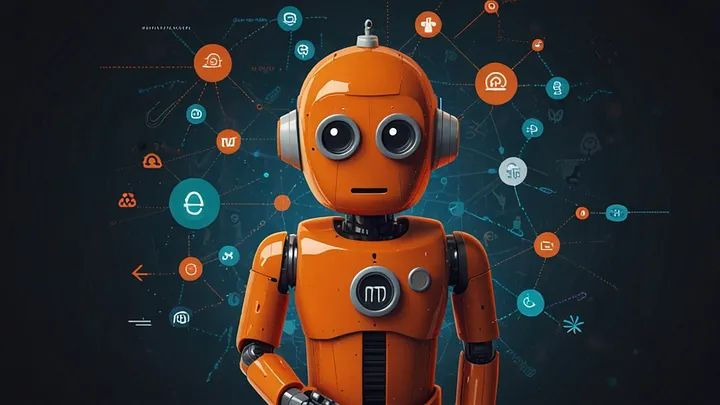
What Is Integrated Automation in Sugar Mills?
At its essence, integrated automation in a sugar mill refers to the seamless connection of various technological systems, each contributing to more efficient, streamlined operations. Through the integration of real-time data collection, advanced control mechanisms, and predictive analytics, automation offers sugar mills the ability to optimize each part of the production cycle—from crushing sugarcane to refining sugar crystals and packaging the final product.
Integrated automation incorporates technologies such as Programmable Logic Controllers (PLCs), Supervisory Control and Data Acquisition (SCADA), Internet of Things (IoT), and robotic systems into a unified control system. These systems are not only responsible for automating processes but also for providing real-time feedback and insight into every facet of the mill’s operations.
Key Components of Integrated Automation:
Sensors: These are the eyes and ears of the automated system. Placed throughout the mill, sensors measure various parameters such as temperature, pressure, flow rates, and moisture content. In sugar mills, sensors monitor key production steps like juice extraction, evaporation, and crystallization, ensuring that everything is functioning within optimal parameters. By providing real-time data, sensors allow for instant adjustments, which enhances operational efficiency.
Programmable Logic Controllers (PLCs): PLCs are responsible for controlling machinery and equipment within the mill. They operate through pre-programmed logic and make real-time decisions based on sensor data. For instance, PLCs control the operation of crushers, boilers, and conveyors, making automated adjustments as needed. The speed, timing, and intensity of each process are dictated by the PLCs, minimizing the need for human intervention and ensuring optimal operations.
Supervisory Control and Data Acquisition (SCADA): SCADA systems provide mill operators with an overview of the entire production process. SCADA integrates data from various sensors, PLCs, and other automation devices into a user-friendly interface, allowing operators to monitor and control operations in real-time. With SCADA, operators can track performance, identify potential issues before they escalate, and make informed decisions to improve mill performance.
Internet of Things (IoT): The IoT expands automation capabilities by connecting sensors and machines to a network, allowing them to communicate and share data. By utilizing IoT devices, sugar mills can implement advanced monitoring systems that enable predictive maintenance, track performance in real-time, and improve energy management. IoT is also crucial in connecting multiple mills in a network, facilitating centralized control across multiple locations.
Robotics and Automated Machines: While not always present in every sugar mill, the use of robotics is on the rise. Automated machines and robots handle tasks like packaging, sorting, and cleaning, making these processes faster and more efficient. These machines reduce the need for human labor, streamline processes, and increase safety. Robots also work in tandem with other automation systems to improve consistency and reduce the risk of contamination.
By integrating these systems, sugar mills can create a smart, interconnected production environment, where every component works together to ensure that the mill operates at peak efficiency.

The Key Benefits of Integrated Automation in Sugar Mills:
Sugar mills stand to gain a wide range of benefits from adopting integrated automation. Not only can it streamline operations and reduce costs, but it can also improve quality control, minimize human error, and enhance overall productivity. Let's explore some of the top benefits of integrating automation into sugar mills:
1. Increased Productivity Through Continuous Operations
One of the most immediate and impactful benefits of automation is the ability to increase productivity. Sugar mills that implement automation systems experience improved throughput because automated processes can run 24/7, without the need for breaks, shifts, or downtime for human workers.
Automation ensures that each part of the process, from crushing to crystallization, operates at optimal speeds, which significantly increases the production output.
For example, automated systems can adjust settings based on real-time data to avoid bottlenecks and improve flow rates. Additionally, automated machinery such as conveyors and crushers work in tandem with each other to maintain a continuous production cycle. As a result, automated mills have been able to increase productivity by 20-30%, depending on the size of the operation.
2. Predictive Maintenance and Reduced Downtime
Unplanned downtime can be a major roadblock for sugar mills, leading to delays in production and significant financial losses. Integrated automation can combat this issue through predictive maintenance. By continuously monitoring key equipment and sensors, automation systems can predict when equipment is likely to fail, allowing for proactive maintenance rather than reactive repairs.
For instance, if an automated system detects that a motor is running hotter than usual or a valve is showing signs of wear, it can trigger an alert to the maintenance team. With predictive maintenance, mills can schedule repairs during non-peak hours, preventing unplanned downtime and ensuring continuous operations. Predictive maintenance has been shown to reduce downtime by as much as 50%, which translates to higher productivity and lower operational costs.
3. Enhanced Energy Efficiency and Cost Savings
Energy costs are a major factor in the operating expenses of sugar mills. Processes such as boiling, evaporation, and crystallization consume significant amounts of energy. Integrated automation helps optimize energy usage by providing real-time insights into energy consumption patterns and adjusting parameters for maximum efficiency.
Automated systems can regulate energy-intensive processes, ensuring that only the necessary amount of energy is used. For example, automated boilers can be adjusted to optimize fuel consumption, reducing wastage. Additionally, heat recovery systems integrated with automation can reclaim heat from exhaust gases, further improving energy efficiency. On average, mills using automation have reported 15-20% reductions in energy consumption, which contributes directly to cost savings and a reduced environmental footprint.

4. Improved Product Quality and Consistency
In the sugar industry, consistency in product quality is paramount. Any variation in quality can result in customer dissatisfaction and financial losses. Integrated automation ensures that every part of the production process is tightly controlled, leading to consistent product quality.
For instance, automated crystallization processes monitor and adjust variables like syrup concentration, temperature, and cooling rates to ensure that the sugar crystals formed are uniform in size and texture.
Since the system continuously checks and corrects parameters, the chances of producing subpar sugar or wasting raw materials are greatly minimized.
Applications of Automation in Sugar Mills:
Brazil’s Leading Sugar Mill Implements Full Automation
A leading sugar mill in Brazil faced challenges related to production inefficiencies, high energy consumption, and inconsistent sugar quality. The mill decided to implement a fully automated control system. Within the first year, the results were remarkable:
Production increased by 25% as automated systems optimized each step of the process, from crushing sugarcane to packaging the final product.
Energy consumption dropped by 15% as boilers, evaporators, and crystallizers were optimized to use less energy while maintaining high production levels.
Sugar quality remained consistent, leading to higher customer satisfaction and improved market positioning.
This example highlights the tangible improvements automation can bring to both the economic and operational aspects of sugar milling.
India’s Sugar Mill Streamlines Processes with Automation:
In India, a large sugar mill faced challenges in managing fluctuating cane inputs and high operational costs. The mill implemented an automated weighing system and upgraded its boiler optimization technology. After the system was installed:
Cane measurement accuracy improved, reducing raw material waste by 10%.
Fuel costs dropped by 20% as the boilers were adjusted to burn fuel more efficiently.
The crystallization process became more reliable, reducing variation in sugar quality.
This case illustrates how automation can not only streamline production processes but also make sugar mills more sustainable by reducing waste and improving resource management.
How to Implement Integrated Automation in Your Sugar Mill:
Implementing integrated automation in a sugar mill is a strategic decision that requires careful planning, investment, and a willingness to embrace change:
1. Assess Your Current Processes
Before embarking on an automation journey, conduct a thorough assessment of your current processes. Identify areas where automation can have the most significant impact—whether it’s in milling, evaporation, crystallization, or packaging. Mapping out the entire production cycle will help you understand where inefficiencies lie and where automation can bring the most value.

2. Choose the Right Technology and Partners
Selecting the right automation technology is crucial for success. Consider working with experienced automation vendors who understand the unique challenges of the sugar industry. They can provide customized solutions based on your mill’s specific needs and requirements. Whether it’s advanced PLCs, SCADA systems, IoT sensors, or robotics, the right technology will make a substantial difference in the efficiency of your mill.
3. Train and Empower Your Workforce
Automation is only as good as the people who operate and maintain it. Therefore, it’s vital to invest in employee training to ensure that workers understand how to interact with new technologies. Provide comprehensive training on new systems, processes, and best practices. This not only helps reduce resistance to change but also empowers employees to operate automation systems effectively.
4. Monitor, Optimize, and Iterate
Once automation is implemented, continuous monitoring and optimization are essential for maintaining performance over time. Use data analytics to evaluate the effectiveness of automation systems, identify bottlenecks, and make adjustments as needed. Automation is a dynamic process, and constant fine-tuning will help you achieve ongoing improvements in efficiency and productivity.
Challenges and Solutions in Implementing Automation:
Despite its numerous benefits, the implementation of integrated automation can come with challenges:
Initial Cost
The upfront cost of automation can be a significant barrier for many sugar mills, particularly smaller operations. However, the long-term cost savings from increased productivity, reduced downtime, and lower energy consumption typically outweigh the initial investment. In many cases, mills begin seeing a return on investment within 2-3 years of automation implementation.
Employee Resistance to Change
Workers may feel apprehensive about automation, particularly if they fear job displacement. To address this, involve employees early in the planning process and provide training to show how automation will make their jobs easier and more efficient. Highlight the safety benefits of automation and reassure workers that automation complements human effort, rather than replacing it.
Technical Expertise
Many sugar mills may not have the in-house expertise to manage these systems. To overcome this, consider partnering with automation vendors who offer ongoing support, training, and troubleshooting services. Additionally, hiring skilled professionals or offering internal upskilling programs will help ensure long-term success.

Conclusion
The sugar industry is evolving, and integrated automation is at the forefront of this transformation. By enhancing productivity, reducing downtime, improving energy efficiency, and ensuring consistent product quality, automation is revolutionizing how sugar mills operate. As the demand for efficiency, sustainability, and high-quality products increases, integrated automation offers a path forward for sugar mills looking to stay competitive in an increasingly challenging environment.
Adopting integrated automation in your sugar mill is not just an investment in technology; it’s an investment in the future of your operations. With careful planning and the right technology, sugar mills can navigate the challenges ahead, boosting productivity while ensuring long-term success and sustainability.
#Sugarcane harvesting automation #Automated sugarcane harvesters #Integrated automation in sugar mills #Sugar mill automation #PLC systems in sugar mills #SCADA systems for sugar mills #IoT in sugar production #Energy efficiency in sugar mills #Predictive maintenance for sugar mills #Sugar mill robotics #Automation in crystallization process #Smart sugar mills #Automated crushing machines #Sugar mill productivity #Automation in sugar production #Mill efficiency through automation #Sugar mill control systems #Real-time data collection in mills #Energy optimization in sugar mills #Boiler automation in sugar mills #Automated packaging systems #Automated sorting in sugar mills #Improved sugar quality through automation #Sugar mill operational cost reduction #Automation for reduced downtime #Crystallization process automation #Sugar mill process optimization #IoT-enabled sugar mills #Advanced automation technology for mills #Sustainable sugar mill operations #Robotic systems in sugar mills
Comments