Ethanol Production: How ERP Systems Make Everything Easier, Smarter, and Better
- hr30522
- Apr 19
- 7 min read
Ethanol is not just a fuel; it’s a vital part of a sustainable energy future. It helps power vehicles, reduces our reliance on fossil fuels, and can be produced from renewable resources like plants. Specifically, ethanol is often made from sugarcane and its byproducts, such as molasses. These products can be turned into high-quality ethanol through a carefully managed and complex process.
However, the journey from raw sugarcane molasses to ethanol is far from simple. Factories need to coordinate many different tasks, follow strict regulations, and deal with an enormous amount of data. This is where ERP (Enterprise Resource Planning) systems step in to help. Think of an ERP system as a smart assistant that helps businesses manage and streamline all their important tasks in one place, making everything run more smoothly and efficiently. In the case of ethanol production, ERP software makes everything more efficient, organized, and compliant with regulations.
In this blog, we’ll dive into how ERP systems can streamline every stage of ethanol production, ensuring smooth operations, higher profits, and better compliance with industry regulations. From raw material tracking to the final product delivery, ERP systems are revolutionizing the way ethanol is produced.

The Challenges of Ethanol Production:
Producing ethanol is not just a matter of turning sugar into alcohol. It’s a highly technical process that involves numerous stages and potential hurdles. The challenges ethanol producers face are numerous and varied, but they can generally be categorized into a few broad areas:
1. Complexity of the Production Process
The process of turning raw materials like sugarcane molasses into ethanol involves multiple steps:
Fermentation: Yeast is added to molasses to convert sugar into alcohol.
Distillation: The alcohol is then separated from the other components through heating and cooling.
Purification: The ethanol is purified to meet the required standards for fuel use.
Each of these stages must be precisely managed to ensure the quality and quantity of the final product. A mistake at any point in the process—whether it’s using the wrong amount of yeast or not monitoring the distillation temperatures properly—can lead to wasted resources, lower ethanol yield, and delays.
2. Regulatory Compliance:
Governments and environmental agencies set strict rules for the production of ethanol. These regulations ensure that ethanol meets quality standards for safety, environmental impact, and production processes. Compliance is not optional—violations can lead to costly fines or even factory shutdowns.
Ethanol producers must track things like emissions, waste disposal, and energy consumption. They also need to provide documentation to prove they’re meeting these requirements. If you don't keep up with these regulations, it could lead to big legal and financial problems.
3. Inventory and Resource Management:
In any manufacturing environment, keeping track of inventory and resources is critical. In ethanol production, this involves raw materials (like molasses), equipment (like fermenters and distillers), and the final product (ethanol). Without proper management, there can be shortages or overstocking, both of which are costly and inefficient.
Furthermore, ethanol production involves handling large quantities of raw materials that have a limited shelf life. If inventory management is not done right, a factory might find itself unable to meet production goals or even face product spoilage, which is a massive loss.
4. Data Overload:
Ethanol production generates an enormous amount of data. Every machine, every batch of ethanol, and every process step generates data—everything from temperatures to chemical composition to labor hours. While data is crucial for decision-making, it’s often overwhelming when not properly organized and analyzed.
The key challenge is not collecting data but making sense of it. Without the right tools, factory managers and decision-makers may struggle to find actionable insights, leading to inefficiencies and missed opportunities.
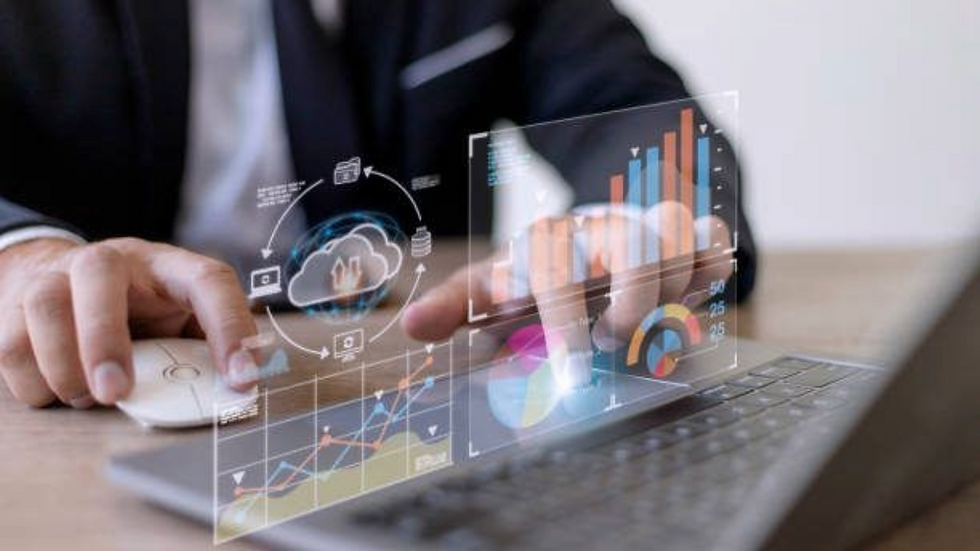
How ERP Systems Solve These Challenges:
ERP systems are built to turn confusion into clarity.. They provide a central platform that integrates all business functions—like production, inventory management, compliance, and financial tracking—into one unified system. Let’s explore how ERP systems specifically help ethanol production factories.
1. Simplifying Complex Processes:
Ethanol production involves many steps, and keeping track of each stage can be difficult. ERP systems can manage these processes seamlessly.
Automated Workflow Management: With an ERP system, production schedules, inventory management, and quality checks can be automated. This reduces human error and ensures that every step happens on time and according to plan.
Real-Time Monitoring: ERP systems allow factory managers to monitor every stage of production in real-time. They can see how much molasses is being processed, how the fermentation is going, and when the distillation process will be completed. This information is updated continuously, helping teams stay on top of the production process.
2. Ensuring Regulatory Compliance:
Ethanol production is a heavily regulated industry, and ERP systems help keep track of compliance with all these rules.
Environmental Tracking: ERP systems help track emissions, energy use, and waste management. These features ensure that factories stay compliant with environmental regulations.
Document Management: ERP systems also help with regulatory paperwork. They store reports and compliance documents in an easy-to-access digital format. This makes it much easier to submit reports to government bodies or during inspections.
Some advanced ERP systems even offer real-time alerts to notify factory managers when something is out of compliance, which allows them to address issues before they become problems.
3. Efficient Inventory Management:
Inventory management can make or break an ethanol factory’s efficiency. ERP systems help manage resources in real-time, making sure that factories never run out of raw materials or overproduce ethanol.
Material Tracking: From raw materials like molasses to final products, ERP systems can track everything in real-time. They show exactly how much molasses is in stock and how much is used in production.
Preventing Stock outs or Overstocking: The system can also forecast inventory needs based on production levels, helping managers ensure they have the right amount of resources without overstocking.
Inventory Optimization: ERP systems help optimize inventory levels, reducing waste, minimizing storage costs, and increasing production efficiency.
4. Turning Data Into Actionable Insights:
Data is only useful when it leads to better decision-making. ERP systems do more than just collect data—they transform it into actionable insights.
Centralized Data: All production-related data is stored in one central location. This means factory managers don’t have to hunt for information in different places.
Advanced Reporting: ERP systems generate detailed reports on everything from production performance to financial analysis. These reports are easy to read and help decision-makers understand where improvements can be made.
Predictive Analytics: Some ERP systems even include predictive analytics that can forecast future trends. For example, based on current production rates and historical data, the ERP can predict when a particular machine might need maintenance, allowing managers to take preventative action.
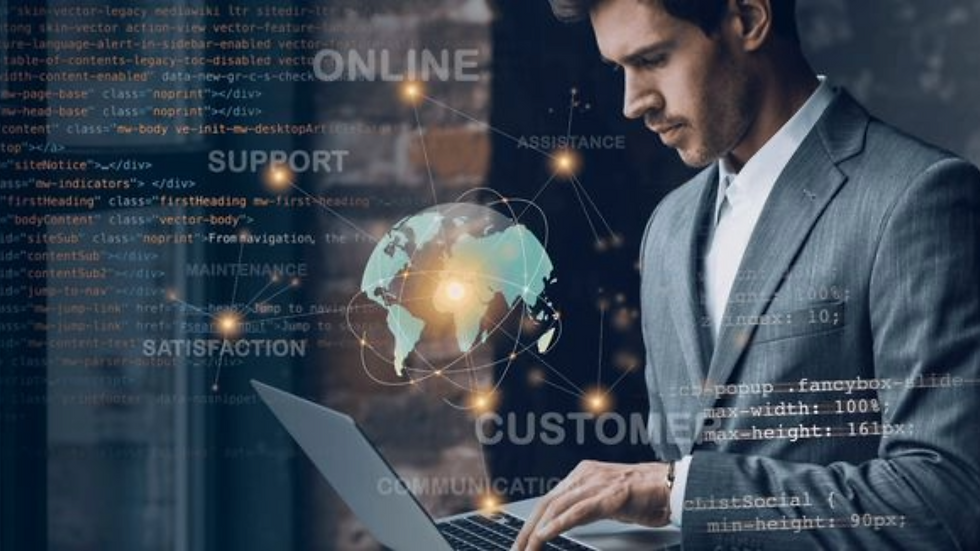
5. Improving Communication and Collaboration:
An ERP system enhances communication across departments. In an ethanol production facility, production, quality control, compliance, and sales departments need to work together seamlessly. ERP systems allow all departments to access the same information in real-time, ensuring that everyone is on the same page.
Real-Time Updates: With all data updated in real time, managers, supervisors, and workers in different departments can collaborate more easily. This helps avoid delays, miscommunication, and errors.
Integrated Systems: ERP systems integrate with other software platforms, like finance or human resources, so managers don’t need to use different tools to track production, payroll, and inventory.
How ERP Transformed Ethanol Production:
A Brazilian Ethanol Plant:
A major ethanol plant in Brazil faced challenges with keeping track of inventory. They were often running out of raw materials or having too much stock that took up valuable space. After implementing an ERP system, they were able to monitor the molasses inventory in real time and forecast when new shipments were needed.
As a result, they were able to avoid running out of stock 30% more often and saved money on storage costs. The system also helped improve production efficiency, allowing them to increase output by 15% without adding new equipment.
A U.S. Ethanol Producer:
In the United States, a large ethanol producer was facing penalties for non-compliance with environmental regulations. They were manually tracking their emissions, waste disposal, and energy usage, but the process was slow and error-prone. After switching to an ERP system, they were able to automate these tracking processes and generate real-time compliance reports.
Within months, they had reduced fines by 40% and improved their environmental score. They also saved money on regulatory costs and improved their reputation with both the government and the public.
How to Choose the Right ERP for Your Ethanol Production:
Choosing the right ERP system is crucial for maximizing the benefits of technology. Here are some important factors to consider when selecting an ERP system for your ethanol production facility:
Industry-Specific Functionality: Ensure that the ERP system is tailored to the needs of the ethanol production industry. Look for features like real-time fermentation tracking, regulatory compliance automation, and supply chain management capabilities.
Scalability: As your production grows, so should your ERP system. Choose a system that can scale with your business and handle increased data and production demands.
User-Friendliness: The ERP system should be user-friendly and simple to navigate. This will reduce training time and improve productivity for employees.
Support and Training: Choose a system with excellent customer support. You’ll want access to technical support and training to help your team get the most out of the software.
The Future of ERP in Ethanol Production:
The future of ERP systems is bright, and the technology is only getting smarter. Here are a few trends that will shape the future of ERP in ethanol production:
Artificial Intelligence (AI): AI will help predict and prevent issues in the production process, from machine failures to supply chain disruptions.
Internet of Things (IoT): IoT devices will connect machines and equipment to the ERP system, providing real-time data on everything from machine performance to environmental conditions.
Sustainability: As sustainability becomes more important, ERP systems will help ethanol producers monitor their environmental impact and optimize resource usage, ensuring a greener future for the industry.
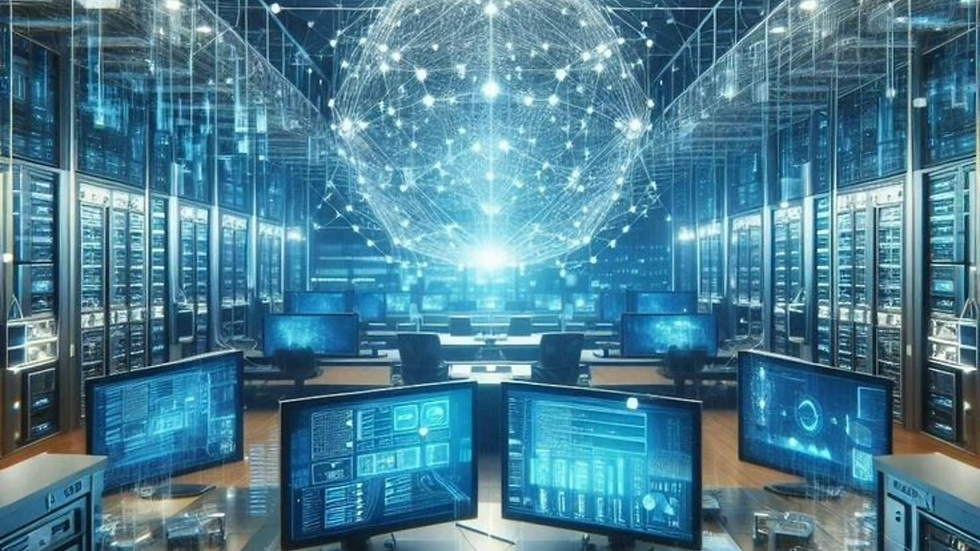
Conclusion:
Ethanol production is a complex and demanding industry that requires careful attention to detail, strict adherence to regulations, and efficient use of resources. ERP systems provide the tools necessary to meet these challenges head-on, helping ethanol producers streamline their operations, reduce costs, and stay compliant with regulations.
If you're in the ethanol business, it’s time to consider implementing an ERP system. Not only will it make your production process more efficient, but it will also give you the competitive edge you need to succeed in a rapidly evolving market. By embracing ERP, you can transform your factory into a smart, sustainable, and profitable powerhouse of the future.
#Ethanol Production ERP Systems #Sugarcane Molasses #ERP Software in Ethanol Production #Ethanol Manufacturing Process #Fermentation Tracking #Distillation Automation #Inventory Management in Ethanol Production #Regulatory Compliance in Ethanol #Real-Time Production Monitoring #ERP for Ethanol Factories #Sustainable Ethanol Production #Sugarcane Ethanol Fuel #Ethanol Plant Optimization #Production Efficiency in Ethanol #ERP Solutions for Ethanol #Reducing Ethanol Production Costs #Quality Control in Ethanol Production #Ethanol Yield Improvement #ERP for Compliance Management #Data-Driven Decision Making #Real-Time Data in Production #ERP System for Resource Planning #Inventory Optimization in Ethanol Production #Ethanol Production Automation
Comments