Managing Change in the Manufacturing Industry: Strategies for Success
- hr30522
- Oct 15, 2024
- 9 min read
Updated: Nov 12, 2024
In the ever-evolving landscape of the manufacturing industry, managing change effectively is crucial for maintaining competitiveness and achieving long-term success. Whether it involves adopting new technologies, implementing process improvements, or navigating organizational restructuring, the ability to manage change can significantly impact a company's operational efficiency and market position. This comprehensive guide explores the strategies for successfully managing change in manufacturing, offering insights into how to handle these transitions smoothly and effectively.
Understanding the Need for Change
Change is a constant in the manufacturing industry, driven by factors such as technological advancements, market demands, regulatory requirements, and competitive pressures. Understanding the need for change is the first step in effectively managing it.

Reasons for Change:
1. Technological Advancements: New technologies such as automation, artificial intelligence (AI), and the Industrial Internet of Things (IIoT) offer opportunities for increased efficiency and innovation. Adopting these technologies can lead to significant improvements in production processes and product quality.
2. Process Improvements: Continuous improvement methodologies like Lean Manufacturing and Six Sigma focus on optimizing processes to reduce waste, enhance productivity, and improve quality. Process improvements can help manufacturers stay competitive and respond to market demands more effectively.
3. Organizational Restructuring: Changes in organizational structure, such as mergers, acquisitions, or internal restructuring, can impact various aspects of the business. Effective management of organizational change is essential for ensuring smooth transitions and maintaining operational stability.
2. Developing a Change Management Strategy
A well-defined change management strategy is essential for guiding the manufacturing organization through periods of transition. This strategy should include planning, communication, and support mechanisms to address potential challenges.
Key Components of a Change Management Strategy
1. Clear Objectives and Goals: Define the objectives and goals of the change initiative. Understanding what you want to achieve will help in setting clear expectations and measuring the success of the change process. Whether it's improving operational efficiency, adopting new technologies, or restructuring the organization, having well-defined goals is crucial.
2. Stakeholder Engagement: Identify and engage key stakeholders who will be impacted by the change. This includes employees, management, suppliers, and customers. Involving stakeholders early in the process helps in gaining their support and addressing their concerns.
3. Change Management Team: Establish a dedicated change management team responsible for overseeing the implementation of the change initiative. This team should include individuals with expertise in project management, communication, and the specific area of change (e.g., technology adoption or process improvement).
4. Communication Plan: Develop a comprehensive communication plan to keep all stakeholders informed about the change. Effective communication is essential for ensuring that everyone understands the purpose of the change, the expected outcomes, and their role in the process. Use multiple channels, such as meetings, emails, and newsletters, to convey information.
5. Training and Support: Provide training and support to employees to help them adapt to the change. This may include workshops, online training programs, and one-on-one coaching. Ensuring that employees have the necessary skills and knowledge is crucial for a successful transition.
6. Monitoring and Evaluation: Implement mechanisms to monitor the progress of the change initiative and evaluate its effectiveness. Regularly review key performance indicators (KPIs) and gather feedback from stakeholders to assess whether the change is achieving the desired outcomes.

Managing Technology Adoption
The adoption of new technologies is a significant driver of change in the manufacturing industry. Embracing technologies such as automation, AI, and IIoT can lead to enhanced productivity, reduced costs, and improved quality.
Strategies for Successful Technology Adoption
1. Conduct a Needs Assessment: Before adopting new technologies, conduct a thorough needs assessment to identify the specific requirements and potential benefits. Evaluate how the technology aligns with your business goals and how it will address current challenges.
2. Pilot Testing: Implement the technology on a small scale before a full-scale rollout. Pilot testing allows you to evaluate the technology’s effectiveness, identify potential issues, and make necessary adjustments. It also provides an opportunity to gather feedback from users and stakeholders.
3. Integration with Existing Systems: Ensure that the new technology integrates seamlessly with existing systems and processes. Compatibility issues can lead to disruptions and inefficiencies. Work with technology vendors and IT professionals to address integration challenges.
4. Change Management Training: Provide training to employees on how to use the new technology effectively. Training should cover both the technical aspects and the changes in workflow or processes. Support employees in adapting to new tools and methods.
5. Continuous Improvement: Monitor the performance of the new technology and seek opportunities for continuous improvement. Regularly assess its impact on productivity, quality, and efficiency. Use data-driven insights to make informed decisions about further enhancements or adjustments.
4. Implementing Process Improvements
Process improvement initiatives, such as Lean Manufacturing and Six Sigma, aim to enhance operational efficiency and reduce waste. Effective management of these initiatives is essential for achieving desired outcomes.
Key Strategies for Process Improvement
1. Define Clear Objectives: Set clear objectives for the process improvement initiative. This includes identifying specific areas for improvement, such as reducing cycle times, minimizing defects, or increasing throughput. Clear objectives help in focusing efforts and measuring success.
2. Engage Employees: Involve employees in the process improvement efforts. Employees who are directly involved in production processes often have valuable insights into inefficiencies and potential solutions. Encourage a culture of continuous improvement and empower employees to contribute ideas.
3. Use Data-Driven Approaches: Leverage data to identify areas for improvement and measure the impact of changes. Use tools such as value stream mapping, root cause analysis, and performance metrics to analyze processes and make data-driven decisions.
4. Implement Incremental Changes: Implement process improvements incrementally rather than making large-scale changes all at once. Incremental changes allow for easier monitoring and adjustment. They also reduce the risk of disrupting operations and enable smoother transitions.
5. Monitor and Review: Continuously monitor the results of process improvement initiatives and review their effectiveness. Gather feedback from employees and stakeholders to identify areas for further improvement. Adjust strategies as needed to achieve ongoing enhancements.
5. Navigating Organizational Restructuring
Organizational restructuring, including mergers, acquisitions, and internal reorganizations, can have significant implications for the manufacturing business. Effective management of restructuring is essential for minimizing disruptions and ensuring a smooth transition.
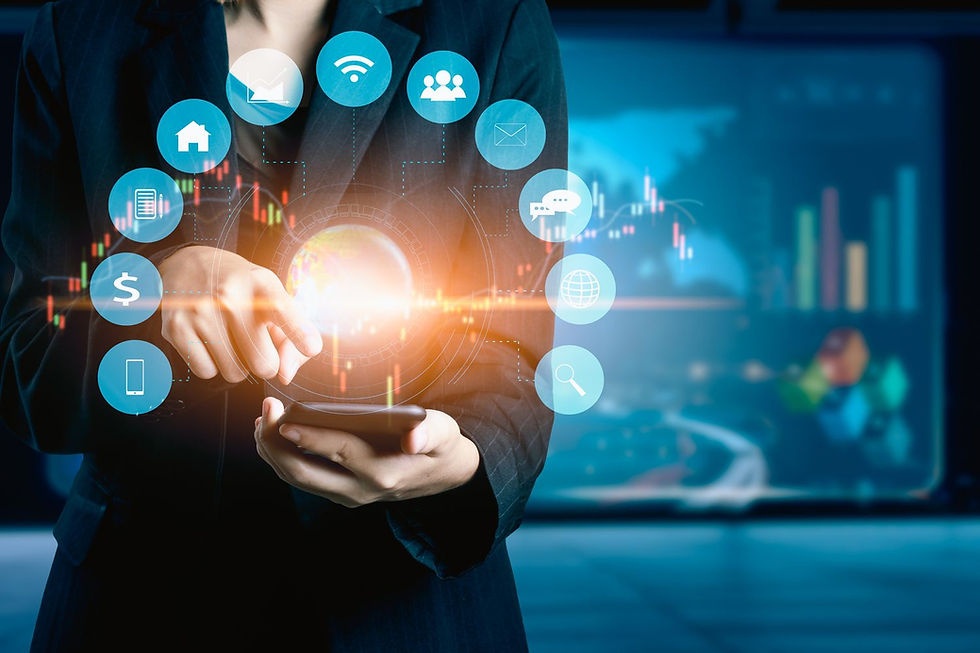
Strategies for Managing Organizational Restructuring:
1. Develop a Comprehensive Plan: Create a detailed plan outlining the objectives, scope, and timeline of the restructuring. The plan should include key milestones, resource requirements, and potential risks. A well-developed plan helps in coordinating efforts and managing expectations.
2. Communicate Transparently: Transparent communication is crucial during organizational restructuring. Keep employees and stakeholders informed about the reasons for the restructuring, the expected outcomes, and how it will impact them. Address concerns and provide regular updates throughout the process.
3. Support Transition: Provide support to employees affected by the restructuring. This may include offering career counseling, training programs, and assistance with job placement. Ensuring that employees feel supported helps in maintaining morale and productivity during the transition.
4. Align Organizational Culture: Align the organizational culture with the new structure and objectives. Cultural alignment helps in fostering a cohesive and motivated workforce. Promote values and behaviors that support the new organizational goals and encourage collaboration.
5. Monitor and Evaluate: Monitor the progress of the restructuring and evaluate its impact on organizational performance. Assess whether the restructuring is achieving the desired outcomes and make adjustments as needed. Gather feedback from employees and stakeholders to identify areas for improvement.
6. Addressing Resistance to Change
Resistance to change is a common challenge in manufacturing and can impede the success of change initiatives. Addressing resistance effectively is essential for ensuring a smooth transition.
Strategies for Addressing Resistance:
1. Understand the Root Causes: Identify the underlying reasons for resistance. This may include fear of job loss, concerns about increased workload, or uncertainty about the future. Understanding the root causes helps in addressing specific concerns and building trust.
2. Involve Employees Early: Involve employees in the change process from the beginning. Seek their input, address their concerns, and provide opportunities for participation. Involvement fosters a sense of ownership and reduces resistance.
3. Provide Clear Information: Offer clear and accurate information about the change initiative. Explain the rationale behind the change, the benefits, and how it will impact employees. Transparency helps in building confidence and reducing uncertainty.
4. Offer Support and Training: Provide support and training to help employees adapt to the change. This includes offering resources, tools, and guidance to ease the transition. Support helps in reducing anxiety and increasing confidence in handling new processes or technologies.
5. Recognize and Reward: Recognize and reward employees who embrace change and contribute positively to the transition. Positive reinforcement helps in reinforcing desired behaviors and encouraging others to follow suit.
Evaluating Success and Continuous Improvement:
Evaluating the success of change initiatives and focusing on continuous improvement are essential for achieving long-term success in the manufacturing industry.
Evaluation and Continuous Improvement Strategies
1. Measure Performance: Use key performance indicators (KPIs) to measure the success of the change initiative. This includes assessing improvements in productivity, quality, and efficiency. Regularly review performance metrics to gauge the impact of the change.
2. Gather Feedback: Collect feedback from employees, stakeholders, and customers to evaluate the effectiveness of the change. Feedback provides valuable insights into the strengths and weaknesses of the change initiative and helps in identifying areas for improvement.
3. Implement Improvements: Use the insights gained from evaluation and feedback to implement further improvements. Continuous improvement involves making incremental changes to enhance processes, technologies, and organizational practices.
4. Celebrate Success: Acknowledge and celebrate the successes achieved through the change initiative. Recognizing achievements boosts morale and reinforces the positive impact of the change. Celebrations also help in maintaining momentum and encouraging continued progress.
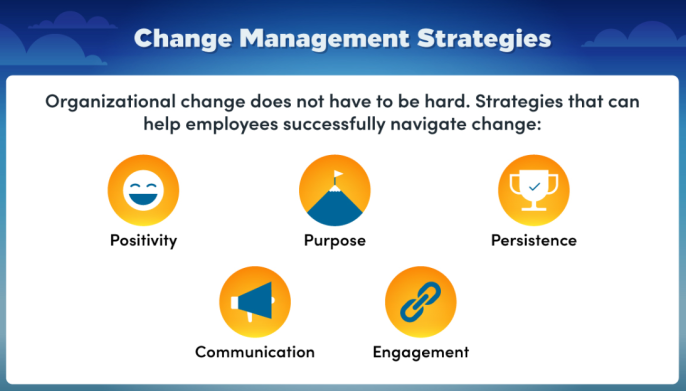
Approaches to Process Improvement
Setting Clear Objectives:
Define specific goals for process improvement, such as reducing cycle times, improving product quality, or increasing throughput. Clear objectives help in focusing efforts and measuring success.
Engaging Employees:
Involve employees in process improvement efforts. Employees who are directly involved in production processes often have valuable insights into inefficiencies and potential solutions. Encourage a culture of continuous improvement and empower employees to contribute ideas.
Leveraging Data-Driven Approaches:
Use data to identify areas for improvement and measure the impact of changes. Tools such as value stream mapping, root cause analysis, and performance metrics help in analyzing processes and making informed decisions.
Implementing Incremental Changes:
Introduce process improvements gradually rather than making large-scale changes all at once. Incremental changes allow for easier monitoring and adjustment, reducing the risk of disruptions and enabling smoother transitions.
Monitoring and Reviewing Performance:
Continuously monitor the results of process improvement initiatives. Gather feedback from employees and stakeholders to assess the effectiveness of changes. Use performance data to identify areas for further improvement and make necessary adjustments.
Navigating Organizational Restructuring
Organizational restructuring involves significant changes to the company's structure, culture, or processes. Effective management of restructuring is essential for ensuring a smooth transition and maintaining operational stability.
Restructuring
Developing a Comprehensive Restructuring Plan:
Create a detailed plan outlining the objectives, scope, and timeline of the restructuring. The plan should include key milestones, resource requirements, and potential risks. A well-developed plan helps in coordinating efforts and managing expectations.
Communicating Transparently:
Communicate openly and honestly with employees and stakeholders about the restructuring. Provide clear information about the reasons for the change, the expected outcomes, and how it will impact individuals and teams. Transparent communication helps in building trust and managing concerns.
Supporting Affected Employees:
Provide support to employees impacted by the restructuring. This may include offering career counseling, training programs, and assistance with job placement. Supporting employees through the transition helps in maintaining morale and productivity.
Aligning Organizational Culture:
Align the organizational culture with the new structure and objectives. Promote values and behaviors that support the new goals and encourage collaboration. Cultural alignment helps in fostering a cohesive and motivated workforce.
Monitoring and Evaluating Outcomes:
Monitor the progress of the restructuring and evaluate its impact on organizational performance. Assess whether the restructuring is achieving the desired outcomes and make adjustments as needed. Gather feedback from employees and stakeholders to identify areas for improvement.
Addressing Resistance to Change
Resistance to change is a common challenge in manufacturing and can hinder the success of change initiatives. Effectively addressing resistance is essential for ensuring a smooth transition.
Understanding Root Causes:
Identify the underlying reasons for resistance, such as fear of job loss, increased workload, or uncertainty about the future. Understanding the root causes helps in addressing specific concerns and building trust.
Involving Employees Early:
Involve employees in the change process from the beginning. Seek their input, address their concerns, and provide opportunities for participation. Early involvement fosters a sense of ownership and reduces resistance.
Providing Clear Information:
Offer clear and accurate information about the change initiative. Explain the rationale behind the change, the benefits, and how it will impact employees. Transparency helps in building confidence and reducing uncertainty.
Offering Support and Training:
Provide support and training to help employees adapt to the change. This includes offering resources, tools, and guidance to ease the transition. Support helps in reducing anxiety and increasing confidence in handling new processes or technologies.
Recognizing and Rewarding Contributions:
Recognize and reward employees who embrace change and contribute positively to the transition. Positive reinforcement helps in reinforcing desired behaviors and encouraging others to follow suit.
Evaluating Success and Embracing Continuous Improvement
Evaluating the success of change initiatives and focusing on continuous improvement are key to achieving long-term success in manufacturing.
Measuring Performance:
Use key performance indicators (KPIs) to measure the success of the change initiative. Assess improvements in productivity, quality, and efficiency. Regularly review performance metrics to gauge the impact of the change.
Gathering Feedback:
Collect feedback from employees, stakeholders, and customers to evaluate the effectiveness of the change. Feedback provides valuable insights into the strengths and weaknesses of the change initiative and helps in identifying areas for improvement.
Implementing Further Improvements:
Use insights gained from evaluation and feedback to implement additional improvements. Continuous improvement involves making incremental changes to enhance processes, technologies, and organizational practices.
Celebrating Successes:
Acknowledge and celebrate successes achieved through the change initiative. Recognizing achievements boosts morale and reinforces the positive impact of the change. Celebrations help in maintaining momentum and encouraging continued progress.

Conclusion
Managing change in the manufacturing industry is a multifaceted endeavor that requires strategic planning, effective communication, and ongoing support. By developing a clear change management strategy, addressing resistance, and focusing on technology adoption, process improvements, and organizational restructuring, manufacturers can navigate transitions successfully. Embracing continuous improvement and evaluating success ensures that change leads to growth and innovation. With the right approach, manufacturing organizations can turn change into an opportunity for enhanced efficiency, competitiveness, and long-term success.
#ChangeManagement #Manufacturing #IndustryInnovation #LeanManufacturing #ContinuousImprovement #AgileManufacturing #Transformation #OperationalExcellence #ManufacturingLeadership #StrategicPlanning #WorkforceDevelopment #ProcessOptimization #ChangeStrategies #Industry40 #SustainableManufacturing #Resilience#CulturalChange #InnovationStrategy #EmployeeEngagement #ManufacturingExcellence #TechnologyIntegration #SupplyChainManagement #FutureOfWork #SkillDevelopment #PerformanceImprovement
Comments