Quality Control in Ethanol Manufacturing: Ensuring Consistency
- hr30522
- Aug 21, 2024
- 8 min read
Updated: Nov 23, 2024
Ethanol production plays a crucial role in various industries, from fuel to beverages and pharmaceuticals. As demand for ethanol grows, maintaining product quality and consistency becomes increasingly important. Quality control (QC) in ethanol manufacturing is vital not only for ensuring that the product meets stringent standards but also for complying with regulatory requirements. In this blog, we will delve into the significance of quality control measures in ethanol production, exploring how they contribute to product consistency and regulatory compliance.
Understanding Ethanol Production
Ethanol, also known as ethyl alcohol, is a versatile substance used in many applications. It is primarily produced through the fermentation of carbohydrates derived from feedstocks such as corn, sugarcane, and other grains. The production process involves several key stages:
Feedstock Preparation: This stage involves milling the raw materials to prepare them for fermentation. The feedstock is ground into a fine powder to increase its surface area and facilitate the conversion of starches into fermentable sugars.
Fermentation: During fermentation, yeast is added to the prepared feedstock to convert the sugars into ethanol and carbon dioxide. This process occurs in large fermentation tanks and typically lasts several days.
Distillation: After fermentation, the ethanol is separated from the fermentation mixture through distillation. This process uses heat to evaporate ethanol, which is then condensed and collected.
Dehydration: The distilled ethanol often contains a small amount of water. Dehydration processes, such as molecular sieve technology, are employed to remove this water and produce high-purity ethanol.
Denaturation (if applicable): For industrial applications, ethanol may be denatured, meaning it is rendered unsuitable for consumption by adding chemicals. This step is necessary to meet regulatory requirements and prevent misuse.
Blending and Packaging: The final ethanol product is blended to meet specific quality standards and then packaged for distribution.
Each of these stages presents opportunities for quality control to ensure that the final product meets required specifications and regulations.

The Role of Quality Control in Ethanol Manufacturing
Quality control in ethanol manufacturing is essential for several reasons:
1. Ensuring Product Consistency
Consistency is key in ethanol production. Consumers and industries rely on ethanol to meet specific standards of purity, concentration, and performance. Inconsistent quality can lead to dissatisfaction, product recalls, and legal issues. Quality control measures ensure that every batch of ethanol meets the same high standards, providing uniformity across all products.
2. Regulatory Compliance
Ethanol production is regulated by various governmental agencies, including the Environmental Protection Agency (EPA), the Food and Drug Administration (FDA), and the Alcohol and Tobacco Tax and Trade Bureau (TTB). These agencies set stringent guidelines for ethanol production, including purity standards, safety protocols, and environmental regulations. Adherence to these regulations is crucial to avoid legal consequences and maintain market access. Quality control helps ensure that all production processes and final products comply with these regulations.
3. Maintaining Ethanol Purity
Purity is a critical aspect of ethanol quality. Even minor impurities can affect the ethanol's performance and safety. Contaminants, whether they come from raw materials, equipment, or the environment, must be identified and eliminated. Quality control measures, including rigorous testing and filtration, help ensure that the final product is free from unwanted substances and meets the required purity levels.
Key Quality Control Measures in Ethanol Manufacturing
Effective quality control in ethanol manufacturing involves a variety of practices and procedures:
1. Process Monitoring and Control Systems
Modern ethanol production relies on advanced control systems to monitor and manage the production process. By continuously monitoring these factors, operators can make timely adjustments to maintain optimal conditions and ensure consistent product quality.
Process Monitoring: Advanced sensors and data collection tools track the status of fermentation, distillation, and dehydration processes. For example, temperature fluctuations during fermentation can affect yeast activity and ethanol yield. Real-time monitoring allows for immediate corrections, preventing deviations from desired conditions.
Control Systems: Automated control systems can adjust process variables based on data inputs. For instance, if a sensor detects that the temperature in a distillation column is too high, the control system can automatically reduce the heat to prevent overheating and ensure that the ethanol is distilled properly.
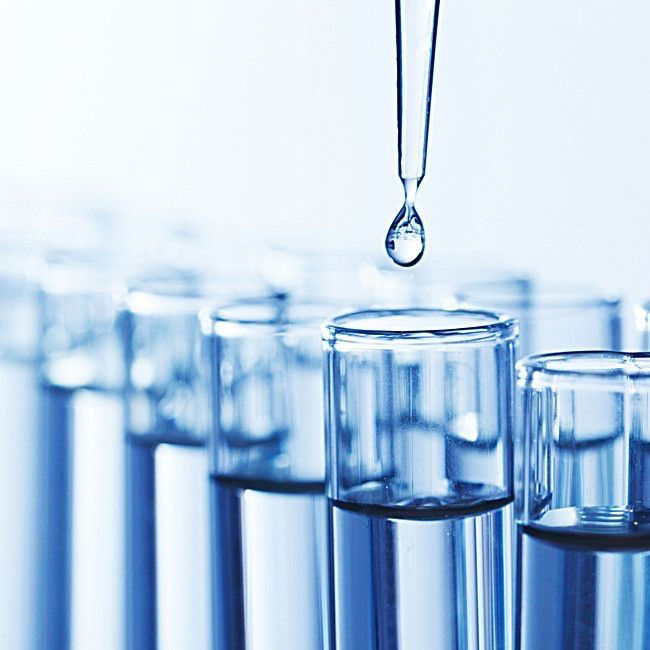
2. Batch Testing and Analytical Methods
Batch testing is a cornerstone of quality control in ethanol production. Each batch of ethanol undergoes a series of tests to verify its quality and adherence to specifications. Analytical methods used in these tests include:
Gas Chromatography (GC): GC is used to analyze the composition of ethanol, determining the concentrations of various compounds. This method is essential for assessing purity and detecting any contaminants.
Mass Spectrometry (MS): MS provides detailed information about the molecular structure of compounds in the ethanol. It is often used in conjunction with GC to identify and quantify impurities.
Alcoholmeters and Refractometers: These instruments measure the concentration of ethanol in the final product. Accurate measurements are critical for ensuring that the ethanol meets regulatory standards and is suitable for its intended use.
3. Contaminant Detection and Removal
Contaminants can come from various sources, including raw materials, equipment, and environmental factors. Quality control measures for contaminant detection and removal include:
Filtration Systems: Filtration systems are used to remove particulate matter and other impurities from the ethanol. These systems can include membrane filters, activated carbon filters, and other technologies designed to ensure high purity.
Chemical Analysis: Regular chemical analysis is performed to detect any residual contaminants. Techniques such as ion chromatography and atomic absorption spectroscopy are used to identify and quantify trace elements and compounds.
Equipment Maintenance: Regular maintenance and cleaning of production equipment help prevent contamination from buildup or residue. Scheduled inspections and servicing ensure that equipment operates efficiently and does not introduce impurities into the product.
4. Process Validation and Optimization
Process validation is essential for confirming that the ethanol production process consistently produces a product that meets quality standards. This involves:
Initial Validation: During the initial stages of production, process validation tests are conducted to establish baseline performance and identify any potential issues.
Ongoing Optimization: Once the process is validated, ongoing optimization is necessary to improve efficiency and address any emerging challenges. This may involve adjusting process parameters, upgrading equipment, or implementing new technologies.
Documentation: Comprehensive documentation of process validation and optimization efforts is crucial for maintaining quality standards and demonstrating compliance with regulatory requirements.
5. Compliance Audits and Documentation
Compliance with regulatory guidelines is a key aspect of quality control. Regular compliance audits are conducted to ensure that all aspects of the production process adhere to industry standards. These audits include:
Internal Audits: Internal audits are performed by the manufacturing company to assess compliance with its own quality control procedures and regulatory requirements. These audits help identify areas for improvement and ensure that all processes are functioning as intended.
External Audits: External audits are conducted by regulatory agencies or third-party organizations to verify compliance with industry regulations. These audits may involve reviewing documentation, inspecting facilities, and evaluating production practices.
Documentation: Maintaining accurate and comprehensive documentation is essential for demonstrating compliance and ensuring transparency. This includes records of testing results, process parameters, equipment maintenance, and audit findings.
Enhancing Quality Control through Technology
Technological advancements have significantly enhanced quality control measures in ethanol manufacturing. Some key innovations include:
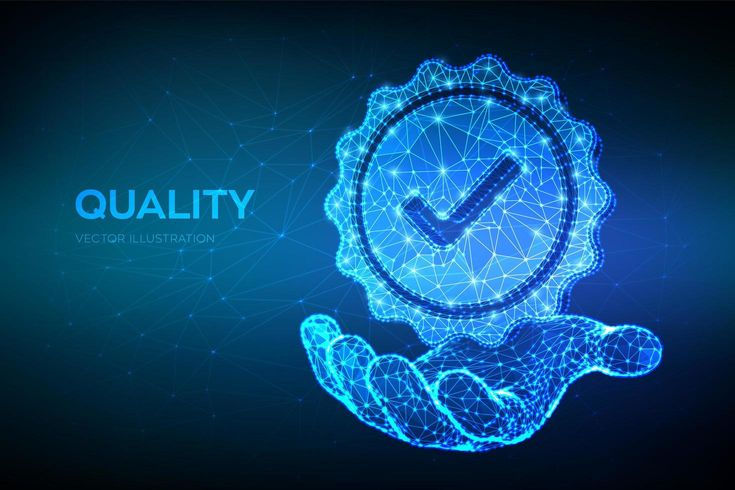
1. Automated Quality Control Systems
Automation has revolutionized quality control by streamlining testing and monitoring processes. Automated systems can perform repetitive tasks with high precision and speed, reducing the risk of human error and increasing overall efficiency.
Automated Testing: Automated testing systems can analyze samples and generate results quickly, allowing for faster decision-making and more frequent testing. This helps ensure that any deviations from quality standards are detected and addressed promptly.
Data Analytics: Advanced data analytics tools provide insights into production trends, process performance, and quality metrics. By analyzing data from multiple sources, manufacturers can identify patterns, predict potential issues, and make informed decisions to improve product quality.
2. Advanced Analytical Techniques
Technological advancements in analytical techniques have improved the accuracy and reliability of quality testing. For example:
High-Performance Liquid Chromatography (HPLC): HPLC is used to separate and analyze compounds in the ethanol. It provides high resolution and sensitivity, making it ideal for detecting impurities and assessing product quality.
Fourier Transform Infrared Spectroscopy (FTIR): FTIR is used to identify chemical bonds and functional groups in the ethanol. It provides valuable information about the composition and purity of the product.
Near-Infrared Spectroscopy (NIRS): NIRS is used for rapid, non-destructive analysis of ethanol composition. It is particularly useful for real-time monitoring and quality control during production.
3. Real-time Data Monitoring
Real-time data monitoring systems provide continuous oversight of the production process. These systems use sensors and data acquisition tools to track process parameters and detect any deviations from desired conditions.
Real-time Alerts: Real-time monitoring systems can generate alerts when process parameters fall outside acceptable ranges. This allows operators to take immediate corrective actions and prevent potential issues from affecting product quality.
Data Integration: Integrating real-time data with control systems enables automatic adjustments to process parameters. For example, if a sensor detects a temperature deviation during fermentation, the control system can adjust the heating element to maintain optimal conditions.
Challenges and Solutions in Quality Control
While quality control is essential, it comes with its own set of challenges. Addressing these challenges requires a proactive approach and effective solutions.
1. Managing Variability in Raw Materials
Variability in raw materials, such as differences in the quality of feedstock, can impact the consistency of ethanol production. To manage this variability:
Supplier Quality Assurance: Establishing strong relationships with suppliers and conducting regular quality assessments of raw materials can help ensure consistency in feedstock quality.
Raw Material Testing: Regular testing of raw materials for key parameters, such as moisture content and starch levels, helps identify and address any variations before they affect the production process.
2.Ensuring Accurate Measurement and Calibration
Accurate measurement and calibration of equipment are critical for maintaining consistent product quality. To ensure accuracy:
Regular Calibration: Equipment used in ethanol production should be calibrated regularly to maintain precision. Calibration protocols should follow manufacturer recommendations and industry standards.
Measurement Verification: Implementing procedures for verifying measurement accuracy, such as cross-checking with reference standards, helps ensure that instruments are functioning correctly.

3. Adapting to Regulatory Changes
Regulatory guidelines for ethanol production may evolve over time, requiring manufacturers to adapt their quality control practices. To stay compliant:
Regulatory Monitoring: Keeping abreast of changes in regulations and industry standards is essential for maintaining compliance. This may involve subscribing to industry publications, attending conferences, and participating in regulatory forums.
Procedure Updates: Updating quality control procedures and documentation to reflect regulatory changes helps ensure that production practices remain aligned with current requirements.
The Role of Continuous Improvement
Quality control is not a static process but one that benefits from continuous improvement. Manufacturers should regularly review and update their quality control measures to incorporate new technologies, address emerging challenges, and enhance overall efficiency. Key aspects of continuous improvement include:
1. Regular Reviews and Updates
Regular reviews of quality control practices and procedures help identify areas for improvement. This may involve analyzing performance metrics, conducting audits, and soliciting feedback from stakeholders.
2. Innovation and Technology Integration
Embracing new technologies and innovations can enhance quality control measures. For example, integrating advanced analytical techniques, automated systems, and real-time monitoring tools can improve accuracy and efficiency.
3. Training and Development
Investing in training and development for staff ensures that they are knowledgeable about the latest quality control practices and technologies. Ongoing training programs can help employees stay updated on industry standards and best practices.
Conclusion
In the ethanol manufacturing industry, quality control is the foundation of product consistency and regulatory compliance. Through rigorous quality control measures—including process monitoring, batch testing, contaminant detection, and compliance audits—manufacturers can ensure that their products meet the highest standards of quality. Technological advancements and a commitment to continuous improvement further enhance the effectiveness of these measures.
As the ethanol industry continues to evolve, maintaining high standards of quality will remain essential. By embracing best practices, leveraging technological innovations, and fostering a culture of continuous improvement, ethanol producers can achieve excellence in every aspect of their production process. The commitment to quality control not only ensures product consistency but also upholds regulatory compliance, ultimately contributing to the success and reputation of the ethanol manufacturing industry.
ManufacturingStandards #ProcessMonitoring #QualityAssurance #EthanolPurity #ProductionEfficiency #BatchTesting#QualityMetrics #EthanolStandards #ComplianceAudits #ProductionUniformity #QualityControlProcedures #EthanolTesting #ProcessOptimization #Regulatory Guidelines #SafetyProtocols #EthanolYield #QualityImprovement #ControlSystems #IndustryStandards #ChemicalAnalysis #ProcessValidation #QualityCheckpoints #EthanolGrades #LaboratoryTesting #ComplianceMonitoring #ProcessIntegrity #QualityBenchmarks #EthanolSpecifications #ConsistencyMeasures #Quality Metrics #ProductionControls #RiskManagement #EquipmentCalibration #QualityDocumentation #Ethanol Concentration #ErrorReduction #ProcessReliability #StandardOperatingProcedures(SOPs) #Ethanol ManufacturingProcess #QualityFeedback #PerformanceIndicators #ComplianceRequirements #ContinuousImprovement
Comments