Rising Production Costs: How ERP Helps Minimize Operational Expenses
- hr30522
- Apr 19
- 6 min read
In today’s fast-paced and competitive business environment, managing production costs is more critical than ever. Rising production costs are a major concern for manufacturers, and businesses are looking for ways to remain competitive while maintaining profitability. One of the most effective ways to minimize operational expenses is by implementing an Enterprise Resource Planning (ERP) system. By providing a comprehensive, integrated approach to managing resources, production, and operations, ERP solutions can significantly enhance efficiency, reduce waste, and lower costs.
In this blog, we will explore how ERP systems help businesses streamline their operations and reduce production costs. From better resource management to improved decision-making, ERP solutions play a key role in improving operational efficiency and driving cost savings. We’ll break down the key features of ERP systems and discuss how these technologies can benefit businesses, ultimately contributing to enhanced profitability and sustainability.
What Are ERP Solutions?
Enterprise Resource Planning (ERP) refers to a suite of integrated software applications that help businesses manage core functions such as finance, human resources, production, supply chain, inventory, and procurement. ERP systems bring together data from different departments into a single system, enabling businesses to gain real-time insights, improve collaboration, and optimize operations.
By consolidating various functions into one centralized platform, ERP systems help eliminate data silos and improve overall visibility. This integration allows businesses to make informed decisions, improve operational workflows, and identify areas where cost savings can be achieved.
ERP solutions are particularly valuable in industries such as manufacturing, where cost control and resource management are vital for staying competitive.

The Impact of Rising Production Costs on Businesses:
In many industries, production costs are on the rise. For manufacturers, this includes the increased cost of raw materials, labor, energy, and transportation. A combination of global supply chain disruptions, rising commodity prices, and inflation has led to higher operational costs for businesses worldwide.
As production costs continue to climb, manufacturers face the challenge of maintaining profitability while keeping prices competitive. Without effective cost-control strategies, businesses risk eroding their profit margins, impacting their bottom line. This is where ERP systems come into play.
By improving resource management, automating tasks, and optimizing production schedules, ERP solutions provide manufacturers with the tools they need to minimize operational expenses. Let’s take a closer look at how ERP systems contribute to reducing production costs.
How ERP Helps Minimize Operational Expenses:
1. Streamlining Resource Management
Resource management is a critical factor in controlling production costs. Without effective resource management, businesses risk overutilizing or underutilizing materials, labor, and equipment, which leads to inefficiencies and unnecessary expenses.
ERP systems enable businesses to track the use of resources in real time, ensuring that materials are available when needed and that production schedules are aligned with resource availability. With ERP’s integrated approach, companies can forecast demand more accurately, optimize inventory levels, and avoid costly stock outs or excess inventory.
By improving inventory management and reducing waste, ERP systems help companies avoid the costs associated with overproduction, storage, and obsolescence.
Key benefits:
Accurate demand forecasting
Reduced waste and excess inventory
Optimized use of raw materials
Reduced storage costs
2. Automating and Optimizing Production Schedules
One of the primary drivers of high production costs is inefficiency in production schedules. In traditional manufacturing setups, production schedules can be manually managed, leading to mistakes, delays, and downtime. These inefficiencies increase labor costs and contribute to unnecessary operational expenses.
ERP solutions can automate production planning and scheduling, ensuring that resources are allocated efficiently and that production processes run smoothly. By analyzing historical data, ERP systems can predict optimal production schedules and help businesses avoid costly bottlenecks.
ERP can integrate with machines and production equipment to monitor performance in real-time. This allows businesses to identify maintenance needs, reduce downtime, and keep production lines running at full capacity, further improving cost efficiency.
Key benefits:
Automated scheduling of production runs
Real-time tracking of machine and equipment status
Reduced downtime and unplanned maintenance
Improved resource utilization

3. Improving Supply Chain Efficiency:
An optimized supply chain is crucial to managing production costs. Delays, inefficiencies, or bottlenecks in the supply chain can significantly impact production schedules and increase costs. ERP solutions provide real-time visibility into supply chain operations, helping businesses streamline the procurement of raw materials and components.
By automating procurement processes and integrating supplier data into the system, ERP systems allow companies to make smarter purchasing decisions. Businesses can track supplier performance, negotiate better pricing, and reduce costs associated with procurement and logistics. Additionally, ERP systems help monitor supplier inventory levels, ensuring that materials are available when needed, and reducing the risk of stock outs that can lead to production delays.
With the integration of data from suppliers, ERP systems allow for more accurate demand forecasting, reducing the need for expedited shipping or emergency orders, both of which can increase costs.
Key benefits:
Improved supplier management
Better negotiation with suppliers for cost savings
Optimized inventory levels
Reduced risk of stock outs or excess inventory
4. Enhancing Workforce Efficiency:
Labor is one of the most significant costs in manufacturing. An efficient workforce can significantly impact the overall cost of production, while labor inefficiencies—such as underutilized staff or overtime—can lead to unnecessary expenses. ERP systems help streamline workforce management by automating scheduling, tracking labor hours, and providing real-time insights into workforce performance.
By automating administrative tasks, such as time tracking and payroll, ERP solutions reduce the amount of manual work required by human resources departments. Moreover, ERP systems provide managers with detailed insights into labor utilization, allowing them to adjust staffing levels and schedules based on actual demand.
By optimizing labor resources, businesses can reduce overtime costs, improve productivity, and better manage workforce expenses.
Key benefits:
Optimized labor scheduling
Reduced overtime and labor costs
Improved employee productivity
Enhanced workforce performance tracking
5. Real-Time Data and Decision-Making:
One of the most valuable features of ERP systems is the ability to provide real-time data and insights across all departments. When businesses have access to accurate, up-to-date information, they can make more informed decisions about production, resource allocation, and cost control.
ERP solutions enable managers to track performance metrics, monitor operational efficiency, and identify areas where costs can be reduced. By analyzing this data, businesses can implement cost-cutting measures quickly and effectively, minimizing waste and improving overall efficiency.
Key benefits:
Improved decision-making through data-driven insights
Better performance tracking and KPI management
Rapid identification of inefficiencies and cost-cutting opportunities
Enhanced ability to respond to market changes

6. Reducing Maintenance Costs:
Unplanned downtime due to equipment failure or maintenance issues can result in significant production losses. ERP systems help manage maintenance schedules and predict when equipment will need servicing, preventing costly breakdowns and reducing downtime.
By integrating with machine sensors and maintenance management modules, ERP systems provide alerts for preventive maintenance, allowing businesses to address issues before they result in costly repairs or unplanned outages.
Key benefits:
Proactive maintenance management
Reduced downtime and repair costs
Increased equipment lifespan
Improved production reliability
ERP Solutions and the Future of Cost Management:
As production costs continue to rise, businesses must adopt more sophisticated and efficient solutions to stay competitive. ERP systems are not only an investment in operational efficiency but also in long-term cost management. With real-time insights, integrated workflows, and automation capabilities, ERP solutions provide businesses with the tools they need to minimize operational expenses, optimize resource management, and boost profitability.
The future of ERP solutions will likely see further integration with emerging technologies such as artificial intelligence (AI) and machine learning (ML), allowing businesses to predict production trends, improve supply chain visibility, and automate decision-making processes. As technology continues to evolve, ERP systems will remain an essential part of an organization’s strategy for managing production costs and staying ahead of the competition.
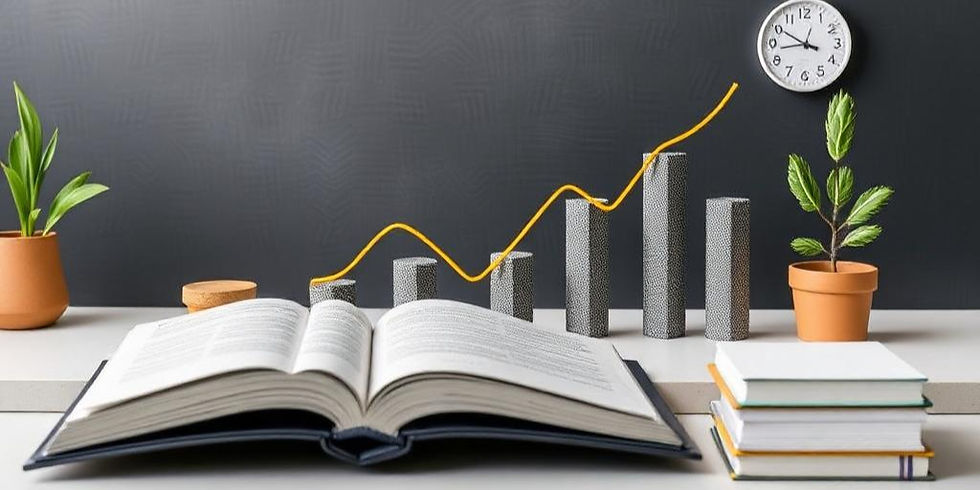
Conclusion:
Rising production costs are a challenge that many businesses face today, but by leveraging ERP systems, companies can minimize these costs and improve overall operational efficiency. From optimizing resource management to automating production schedules, ERP solutions offer a comprehensive approach to reducing waste, improving productivity, and cutting unnecessary expenses.
With the right ERP system in place, businesses can enhance profitability, streamline processes, and navigate the challenges of rising production costs in today’s competitive market.
ERP (Enterprise Resource Planning) systems provide an effective solution by streamlining processes, improving resource management, and enhancing decision-making. By integrating key business functions such as procurement, inventory management, and finance, ERP systems help businesses reduce waste, improve efficiency, and minimize operational expenses. Furthermore, real-time data and analytics offered by ERP allow for better forecasting, cost control, and proactive decision-making. Ultimately, ERP not only helps businesses stay competitive but also positions them to thrive in an environment of rising production costs.
Commentaires