In the dynamic landscape of modern manufacturing, effective risk management is crucial to maintaining operational efficiency and safeguarding against potential disruptions. Manufacturing organizations face a variety of risks, including supply chain disruptions, equipment failures, and market volatility. Addressing these risks requires a comprehensive approach to risk identification, risk assessment, and risk mitigation. This blog explores common manufacturing risks and provides strategies for mitigating them to ensure a resilient and robust manufacturing operation.
Understanding Risk Management in Manufacturing
Risk Management in manufacturing involves identifying potential threats that could impact operations, assessing their likelihood and potential impact, and implementing strategies to mitigate these risks. A well structured risk management framework helps organizations anticipate and prepare for challenges, reducing the likelihood of disruptions and enhancing overall operational stability.
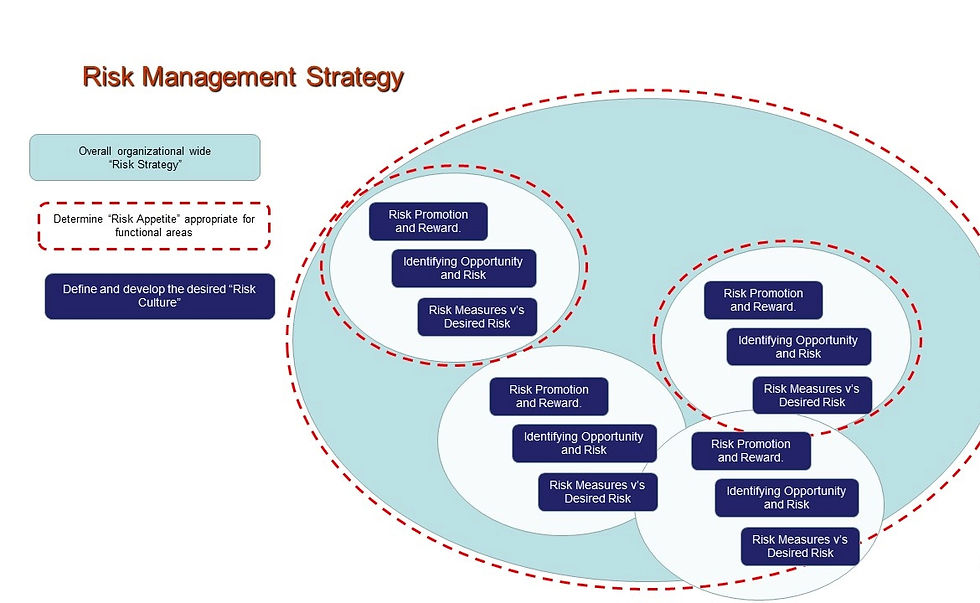
Common Risks in Manufacturing
1. Supply Chain Disruptions
Supply Chain Disruptions are a significant risk for manufacturing organizations, often leading to delays, increased costs, and reduced production capacity. Common causes of supply chain disruptions include:
Supplier Reliability Issues: Dependence on single or unreliable suppliers can lead to shortages and delays in receiving critical materials.
Transportation Failures: Disruptions in transportation, such as delays or accidents, can affect the timely delivery of raw materials and finished products.
Global Events: Events such as natural disasters, geopolitical conflicts, or pandemics can severely impact global supply chains.
Mitigation Strategies:
Diversify Suppliers: Avoid overreliance on a single supplier by developing relationships with multiple suppliers for critical materials. This diversification reduces the risk of shortages and delays.
Build Inventory Reserves: Maintain safety stock or buffer inventory to cushion against supply chain interruptions. This approach provides a buffer while alternative supply sources are sought.
Implement Advanced Planning Systems: Utilize supply chain management software to enhance visibility, track shipments, and predict potential disruptions. Advanced planning systems facilitate better decision making and proactive responses.
2. Equipment Failures
Equipment Failures can lead to significant production downtime, increased maintenance costs, and reduced product quality. Equipment failures may result from:
Wear and Tear: Ongoing use of machinery and equipment can lead to wear and tear, resulting in breakdowns and malfunctions.
Lack of Maintenance: Inadequate or irregular maintenance schedules can exacerbate equipment issues and lead to unexpected failures.
Technological Obsolescence: Aging equipment may become obsolete and less reliable, impacting production efficiency.
Mitigation Strategies:
Implement Preventive Maintenance: Establish a preventive maintenance schedule to regularly inspect and service equipment. Preventive maintenance helps identify and address potential issues before they lead to failures.
Utilize Predictive Maintenance Technologies: Adopt predictive maintenance technologies, such as sensors and data analytics, to monitor equipment performance and predict potential failures. Predictive maintenance enables timely interventions and reduces unplanned downtime.
Invest in Equipment Upgrades: Regularly evaluate and upgrade equipment to incorporate the latest technology and improve reliability. Investing in modern equipment enhances performance and reduces the risk of obsolescence.
3. Market Volatility
Market Volatility refers to fluctuations in market conditions, such as changes in demand, prices, and competition, which can impact manufacturing operations. Key factors contributing to market volatility include:
Economic Fluctuations: Economic downturns or recessions can lead to reduced demand for products, affecting production levels and profitability.
Price Instability: Volatile raw material prices can impact production costs and margins, leading to financial uncertainty.
Competitive Pressures: Increased competition or changes in consumer preferences can influence market share and pricing strategies.
Mitigation Strategies:
Conduct Market Research: Regularly conduct market research to understand industry trends, consumer preferences, and competitive dynamics. Market research provides valuable insights for adapting to changing market conditions.
Implement Flexible Production Systems: Design production systems to be flexible and adaptable to changes in demand. Flexible manufacturing systems allow for quick adjustments in production volumes and product variations.
Develop Financial Reserves: Build financial reserves to cushion against market fluctuations and economic downturns. Adequate financial reserves provide stability and enable companies to weather periods of volatility.

Risk Identification and Assessment:
Risk Identification involves recognizing potential risks that could impact manufacturing operations. Risk Assessment evaluates the likelihood and potential impact of identified risks. Both processes are essential for developing effective risk mitigation strategies.
1. Risk Identification
Identifying risks involves a thorough analysis of various aspects of manufacturing operations, including:
Operational Processes: Assessing internal processes and workflows to identify potential risks and vulnerabilities.
Supply Chain: Evaluating the entire supply chain, including suppliers, logistics, and transportation, to identify potential points of failure.
Market Factors: Analyzing external market conditions, including economic trends, regulatory changes, and competitive pressures.
Techniques for Risk Identification:
Risk Brainstorming: Engage cross functional teams in brainstorming sessions to identify potential risks and vulnerabilities. Collaborative discussions help uncover a wide range of potential risks.
SWOT Analysis: Conduct a SWOT (Strengths, Weaknesses, Opportunities, Threats) analysis to identify internal and external factors that could impact manufacturing operations.
Risk Surveys: Use surveys and questionnaires to gather input from employees, suppliers, and stakeholders regarding potential risks and concerns.
2. Risk Assessment
Risk assessment involves evaluating the likelihood and impact of identified risks to prioritize mitigation efforts. Key steps in risk assessment include:
Risk Probability: Assessing the likelihood of each identified risk occurring. Risks with higher probabilities should be prioritized for mitigation.
Risk Impact: Evaluating the potential impact of each risk on manufacturing operations, including financial, operational, and reputational impacts.
Risk Matrix: Use a risk matrix to categorize risks based on their probability and impact. This visual tool helps prioritize risks and allocate resources for mitigation.
Techniques for Risk Assessment:
Quantitative Analysis: Use quantitative methods, such as statistical analysis and modeling, to assess the probability and impact of risks. Quantitative analysis provides datadriven insights for risk management.
Qualitative Analysis: Conduct qualitative assessments, such as expert judgment and scenario analysis, to evaluate risks based on experience and judgment. Qualitative analysis complements quantitative methods and provides additional context.
Mitigation Strategies and Risk Management Framework
Mitigation Strategies involve implementing measures to reduce the likelihood and impact of identified risks. A well defined Risk Management Framework guides the development and implementation of these strategies.
1. Developing a Risk Management Framework
A robust risk management framework includes the following components:
Risk Management Policy: Establish a formal risk management policy that outlines the organization's approach to risk management, including roles, responsibilities, and procedures.
Risk Management Plan: Develop a comprehensive risk management plan that includes risk identification, assessment, mitigation, and monitoring strategies. The plan should be aligned with organizational goals and objectives.
Risk Management Team: Form a dedicated risk management team responsible for overseeing risk management activities and ensuring the implementation of mitigation strategies.
2. Implementing Risk Mitigation Strategies
Mitigation Strategies vary depending on the type and severity of risks. Common mitigation strategies include:
Risk Avoidance: Altering processes or practices to avoid the risk altogether. For example, diversifying suppliers to avoid dependency on a single source.
Risk Reduction: Implementing measures to reduce the likelihood or impact of risks. For example, adopting preventive maintenance to reduce equipment failures.
Risk Transfer: Shifting the risk to a third party through insurance or contractual agreements. For example, purchasing insurance to cover potential financial losses from supply chain disruptions.
Risk Acceptance: Accepting the risk when the potential impact is manageable and the cost of mitigation outweighs the benefits. For example, accepting minor fluctuations in market prices if they do not significantly impact profitability.
3. Monitoring and Reviewing Risks
Continuous monitoring and review of risks are essential for maintaining an effective risk management process. Key activities include:
Regular Risk Reviews: Conduct regular reviews of the risk management framework and risk mitigation strategies to ensure their effectiveness. Update the framework as needed based on changes in operations or external factors.
Risk Monitoring Systems: Implement risk monitoring systems to track key risk indicators and early warning signs. Monitoring systems provide real time insights into potential risks and allow for timely interventions.
Feedback and Improvement: Gather feedback from stakeholders and incorporate lessons learned from risk events to continuously improve the risk management process. Regularly update risk management practices based on new insights and experiences.
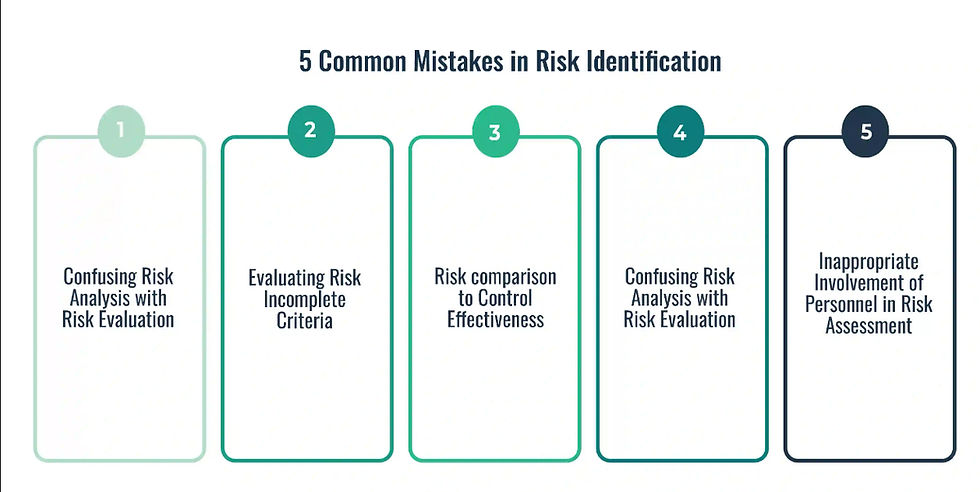
Supplier Reliability Issues:
Dependence on a single or unreliable supplier can lead to material shortages or delays. For example, if a critical supplier faces financial difficulties or production issues, it can halt your entire production line.
Transportation Failures: Disruptions in transportation, such as delays due to logistical errors, natural disasters, or accidents, can affect the timely delivery of raw materials and finished products.
Global Events: Events such as pandemics, geopolitical conflicts, or natural disasters can severely impact global supply chains, causing widespread delays and shortages.
Mitigation Strategies:
Diversify Suppliers: Avoid over-reliance on a single supplier by developing relationships with multiple suppliers for critical materials. This diversification reduces the risk of disruptions and ensures a more stable supply chain.
Build Inventory Reserves: Maintain safety stock or buffer inventory to absorb the impact of supply chain interruptions. This strategy provides a buffer while alternative supply sources are identified and secured.
Implement Advanced Planning Systems: Utilize advanced supply chain management software to enhance visibility, track shipments, and predict potential disruptions. Tools like Enterprise Resource Planning (ERP) systems offer real-time insights and facilitate proactive decision-making
Wear and Tear:
Continuous use of machinery and equipment leads to wear and tear, resulting in breakdowns and malfunctions. For example, aging machinery may suffer from decreased efficiency and reliability.
Lack of Maintenance: Inadequate or irregular maintenance schedules can exacerbate equipment issues, leading to unexpected failures and costly repairs. For instance, failing to regularly lubricate machine parts can result in increased friction and potential breakdowns.
Technological Obsolescence: Older equipment may become obsolete and less reliable over time, impacting production efficiency. Technology advances can render older systems less effective compared to newer, more efficient models.
Mitigation Strategies:
Implement Preventive Maintenance: Establish a comprehensive preventive maintenance program to regularly inspect and service equipment. Preventive maintenance involves scheduled inspections, cleaning, and repairs to address potential issues before they result in failures.
Utilize Predictive Maintenance Technologies: Adopt predictive maintenance technologies, such as sensors and data analytics, to monitor equipment performance and predict potential failures. By analyzing data from equipment sensors, manufacturers can detect early warning signs of issues and schedule maintenance proactively.
Invest in Equipment Upgrades: Regularly evaluate and invest in new equipment that incorporates the latest technology and features. Modern equipment enhances performance, reduces the risk of obsolescence, and improves overall reliability.
Market Volatility involves fluctuations in market conditions that can impact manufacturing operations, including changes in demand, prices, and competitive dynamics. Factors contributing to market volatility include:
Economic Fluctuations: Economic downturns or recessions can lead to reduced demand for products, affecting production levels and profitability. For instance, during economic slowdowns, consumers may cut back on spending, leading to decreased demand for manufactured goods.
Price Instability: Volatile raw material prices can affect production costs and profit margins. For example, sudden increases in the cost of essential materials like steel or oil can significantly impact manufacturing costs.
Competitive Pressures: Increased competition or changes in consumer preferences can influence market share and pricing strategies. Competitive pressures may require manufacturers to adapt their product offerings or pricing strategies to remain competitive.
Mitigation Strategies:
Conduct Market Research: Regularly conduct market research to understand industry trends, consumer preferences, and competitive dynamics. Market research provides valuable insights for adapting to changing market conditions and making informed business decisions.
Implement Flexible Production Systems: Design production systems to be flexible and adaptable to changes in demand. Flexible manufacturing systems allow for quick adjustments in production volumes, product variations, and operational processes.
Develop Financial Reserves: Build financial reserves to cushion against market fluctuations and economic downturns. Adequate financial reserves provide stability and enable manufacturers to navigate periods of volatility without compromising operations.
Operational Processes:
Assessing internal processes and workflows to identify potential risks and vulnerabilities. For example, evaluating production processes to identify potential bottlenecks or inefficiencies.
Supply Chain: Evaluating the entire supply chain, including suppliers, logistics, and transportation, to identify potential points of failure. For example, assessing the reliability of suppliers and the potential impact of transportation delays.
Market Factors: Analyzing external market conditions, including economic trends, regulatory changes, and competitive pressures. For example, monitoring changes in consumer preferences and their potential impact on demand.
Techniques for Risk:
Risk Brainstorming: Engage cross-functional teams in brainstorming sessions to identify potential risks and vulnerabilities. Collaborative discussions help uncover a wide range of potential risks from different perspectives.
SWOT Analysis: Conduct a SWOT (Strengths, Weaknesses, Opportunities, Threats) analysis to identify internal and external factors that could impact manufacturing operations. SWOT analysis helps in understanding both internal capabilities and external challenges.
Risk Surveys: Use surveys and questionnaires to gather input from employees, suppliers, and stakeholders regarding potential risks and concerns. Surveys provide valuable insights from those directly involved in or affected by manufacturing processes.
Risk assessment involves evaluating the likelihood and impact of identified risks to prioritize mitigation efforts. Key steps in risk assessment include:
Risk Probability: Assessing the likelihood of each identified risk occurring. Risks with higher probabilities should be prioritized for mitigation. For example, frequent supply chain disruptions may warrant more immediate attention than infrequent occurrences.
Risk Impact: Evaluating the potential impact of each risk on manufacturing operations, including financial, operational, and reputational impacts. For example, a major equipment failure may have significant operational and financial consequences.
Risk Matrix: Use a risk matrix to categorize risks based on their probability and impact. This visual tool helps prioritize risks and allocate resources for mitigation. Risks are often classified into categories such as low, medium, or high based on their likelihood and potential impact.
Techniques for Assessment:
Quantitative Analysis: Use quantitative methods, such as statistical analysis and modeling, to assess the probability and impact of risks. Quantitative analysis provides data-driven insights for risk management and helps in making informed decisions.
Qualitative Analysis: Conduct qualitative assessments, such as expert judgment and scenario analysis, to evaluate risks based on experience and judgment. Qualitative analysis complements quantitative methods and provides additional context and insights

Conclusion
Risk Management in Manufacturing is a critical component of ensuring operational resilience and stability. By identifying and mitigating common risks such as supply chain disruptions, equipment failures, and market volatility, manufacturers can enhance their ability to respond to challenges and maintain high levels of efficiency and quality.
A comprehensive risk management approach involves effective risk identification, risk assessment, and the implementation of targeted risk mitigation strategies. By developing a robust risk management framework and continuously monitoring and reviewing risks, manufacturers can better navigate uncertainties and achieve long term success.
#RiskManagement #Manufacturing #SupplyChain #OperationalExcellence #QualityControl #ManufacturingRisk #SafetyFirst #ProcessImprovement #RiskAssessment#LeanManufacturing #Industry40 #ContinuousImprovement #ProductionSafety #BusinessContinuity #ManufacturingExcellence #RiskMitigation #SupplierRisk #CrisisManagement #OperationalRisk #ManufacturingStrategy #RiskAnalysis #BusinessRisk #InventoryManagement #ProductionPlanning #QualityAssurance #ProcessRisk
댓글