In the rapidly evolving world of manufacturing, effective supply chain management is crucial for maintaining competitive advantage and operational efficiency. With increasing global competition, fluctuating demand, and complex logistics networks, manufacturers must adopt best practices to streamline their operations, reduce costs, and enhance overall productivity. This comprehensive guide will delve into strategies for optimizing supply chain management in manufacturing, covering key areas such as sourcing, logistics, and inventory control.
Understanding Supply Chain Management in Manufacturing:
Supply Chain Management (SCM) refers to the coordination and management of activities involved in the production and distribution of goods, from raw material acquisition to the final delivery of products to consumers. In manufacturing, effective SCM is essential for ensuring that each link in the supply chain—sourcing, logistics, and inventory management—functions seamlessly to support production goals and meet customer demands.
Sure! Here’s a rewritten version of your blog content that maintains the essence while presenting it differently.
With heightened global competition, variable market demands, and intricate logistics systems, manufacturers are compelled to implement effective strategies that enhance productivity, minimize costs, and streamline processes. This guide explores innovative approaches to optimizing supply chain management within manufacturing, focusing on key elements like sourcing, logistics, and inventory management.

The Role of Supply Chain Management in Manufacturing
Supply Chain Management encompasses the oversight and coordination of all activities involved in the lifecycle of a product—from sourcing raw materials to delivering the finished product to consumers. For manufacturers, efficient SCM is vital for ensuring that each component of the supply chain operates smoothly, meeting production targets and customer expectations.
A well-structured supply chain can significantly lower expenses, elevate product quality, enhance customer satisfaction, and fortify competitive advantages. To achieve these outcomes, manufacturers need to adopt best practices across various domains: sourcing, logistics, and inventory management.
Best Practices for Sourcing
1.Strategic Sourcing
Embracing a strategic approach to sourcing means selecting suppliers with a long-term vision rather than just focusing on immediate costs. This involves assessing potential suppliers based on quality, reliability, pricing, and innovation capabilities. Building strong partnerships can lead to better terms, consistent quality, and enhanced supply chain resilience.
2.Supplier Relationship Management (SRM)
Establishing robust relationships with suppliers is key to successful SCM. Regularly communicating, reviewing performance, and collaboratively addressing challenges helps foster trust and align supplier capabilities with manufacturing needs. Setting clear expectations and utilizing performance metrics can drive continuous improvement.
3.Diversifying Suppliers
Sole reliance on one supplier can be risky, exposing manufacturers to potential disruptions and price changes. By diversifying their supplier base, companies can create a more resilient supply chain that can better adapt to fluctuations in market conditions and reduce the impact of disruptions.
4.Cost Analysis and Negotiation
Conducting comprehensive cost analyses and negotiating favorable terms are crucial for effective sourcing. Manufacturers should evaluate the total cost of ownership, which includes purchase price, transportation, and inventory costs. Engaging in negotiations for better terms, such as volume discounts, can lead to significant savings.
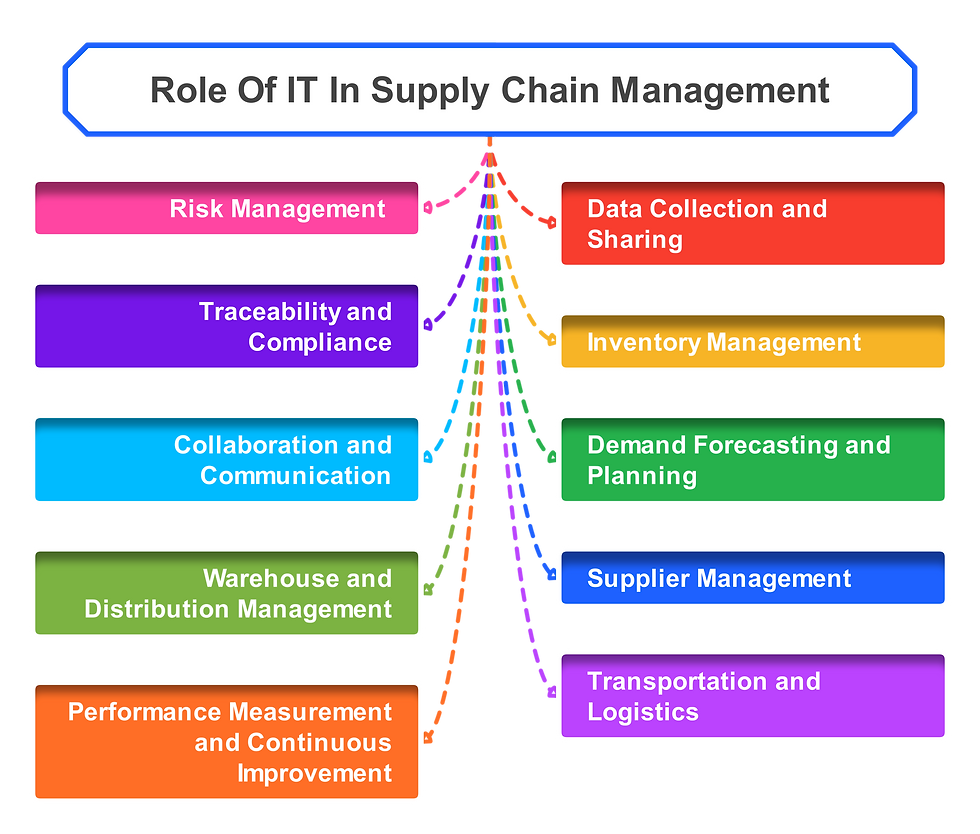
Best Practices for Logistics Management
1.Transportation Efficiency
Effective transportation management is vital for optimizing logistics. Utilizing advanced transportation management systems (TMS) can enhance route planning and carrier selection. Real-time tracking and data analytics can improve delivery accuracy while minimizing transportation costs.
2.Comprehensive Supply Chain Visibility
Achieving end-to-end visibility in the supply chain allows manufacturers to monitor inventory levels and shipment statuses in real time. Technologies like IoT sensors, RFID, and blockchain provide critical insights that enable proactive responses to potential issues and enhance customer service.
3.Lean Manufacturing and JIT
Implementing Lean Manufacturing and Just-In-Time (JIT) methodologies can greatly improve logistics efficiency. Lean practices focus on minimizing waste and optimizing processes, while JIT ensures that inventory levels are closely aligned with actual demand, reducing carrying costs and lead times.
4.Proactive Risk Management
Identifying potential risks in the supply chain and developing contingency plans is essential for maintaining continuity. Regular risk assessments can help manufacturers prepare for various scenarios, ensuring they can quickly adapt to unforeseen challenges.
Best Practices for Inventory Control
1.Demand Forecasting
Accurate forecasting is fundamental for effective inventory management. By analyzing historical sales data and market trends, manufacturers can predict future demand more reliably. Advanced forecasting tools, including machine learning algorithms, can enhance precision in these predictions.
2.Optimizing Inventory Levels
Balancing inventory to meet demand while minimizing costs is crucial. Techniques such as Economic Order Quantity (EOQ), safety stock calculations, and ABC analysis can help determine optimal inventory levels, ensuring that resources are not wasted.
3.Automation in Inventory Management
Automation can streamline inventory processes and improve accuracy. Utilizing warehouse management systems (WMS) and automated tracking solutions helps reduce human error and provides real-time insights into inventory status, facilitating better decision-making.
4.Continuous Improvement
A commitment to continuous improvement is vital for effective inventory control. Regularly reviewing performance metrics—like inventory turnover and carrying costs—can highlight areas for enhancement, ensuring that inventory practices evolve with changing market conditions.

Integrating Supply Chain Best Practices
1.Leveraging Technology
Integrating cutting-edge technologies into SCM can lead to significant efficiency gains. Tools such as cloud computing, big data analytics, and AI can enhance decision-making and streamline processes, driving better overall performance.
2.Fostering Collaboration
Strong collaboration and communication with all supply chain partners are crucial for achieving optimal results. Joint planning and forecasting initiatives can align objectives and enhance supply chain performance.
3.Emphasizing Sustainability
As sustainability becomes increasingly important, manufacturers should consider the environmental impact of their supply chain operations. Implementing eco-friendly practices not only supports corporate responsibility but can also enhance brand reputation.
4.Investing in Training
Ongoing training and professional development for supply chain teams are essential for successful implementation of best practices. Keeping staff informed about industry trends and new technologies ensures they can effectively adapt to the evolving landscape.
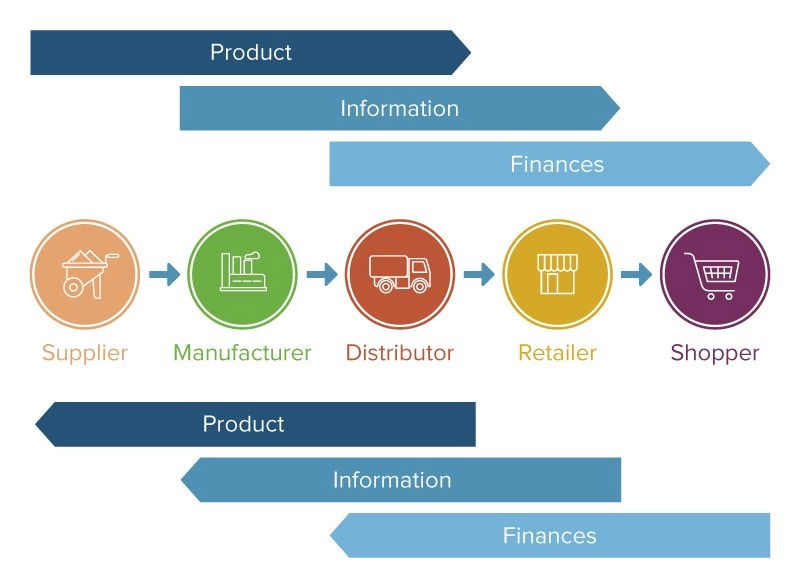
At its core, Supply Chain Management involves the comprehensive coordination of all activities that contribute to the production and distribution of goods. This includes everything from sourcing raw materials to delivering finished products to end-users. In the manufacturing industry, effective SCM ensures that each segment of the supply chain operates in harmony, aligning with production objectives and satisfying customer requirements.
A well-executed supply chain strategy can yield significant benefits, including reduced operational costs, improved product quality, heightened customer satisfaction, and an enhanced competitive position in the marketplace. However, achieving these outcomes requires a strategic and systematic approach, with best practices established in critical areas such as sourcing, logistics, and inventory control.
Implementing Strategic Sourcing Initiatives
Strategic sourcing is a proactive approach that emphasizes long-term supplier relationships over short-term transactional engagements. Manufacturers should evaluate potential suppliers not just on price but on a range of factors including quality, reliability, innovation capabilities, and alignment with long-term business goals. By prioritizing strategic partnerships, manufacturers can negotiate more favorable terms, secure a consistent supply of quality materials, and create a more resilient supply chain.
Supplier Evaluation and Selection: Establish criteria that reflect your company’s specific needs and long-term vision. Regularly reassess suppliers to ensure they continue to meet these standards.
Nurturing Long-Term Relationships: Build partnerships through ongoing communication, joint initiatives, and mutual support, fostering trust and collaboration that can benefit both parties
Enhancing Supplier Relationship Management (SRM)Effective Supplier Relationship Management is crucial for maintaining strong and productive relationships with suppliers. By implementing systematic SRM practices, manufacturers can ensure that suppliers are aligned with their operational objectives and performance expectations.
Performance Monitoring: Develop key performance indicators (KPIs) to regularly assess supplier performance across various metrics, such as delivery accuracy, quality compliance, and responsiveness to issues.
Feedback and Improvement: Create structured feedback mechanisms to communicate supplier performance and encourage continuous improvement. This includes conducting performance reviews and working collaboratively to resolve any challenges.
Diversification of Suppliers Relying on a single supplier can expose manufacturers to significant risks, including supply interruptions and price volatility. To counteract these risks, it’s prudent to diversify the supplier base.
Establishing a Supplier Network: Identify and engage with multiple suppliers for critical materials. This approach not only enhances supply chain resilience but also provides leverage during negotiations.
Ongoing Supplier Assessment: Regularly evaluate the financial health and operational capacity of suppliers to mitigate risks associated with disruptions.
Conducting Comprehensive Cost Analysis and Negotiation A detailed understanding of costs is vital for effective sourcing. Manufacturers should focus on the total cost of ownership (TCO) rather than just initial purchase prices.
Total Cost Evaluation: Analyze all costs associated with procurement, including shipping, handling, and potential risks. This holistic view can inform better sourcing decisions.
Strategic Negotiation: Engage suppliers in negotiations that encompass not only price but also payment terms, volume discounts, and lead times, ultimately leading to more favorable Logistics Management.
Optimizing Transportation Management Efficient transportation management is integral to successful logistics operations. It involves the planning, execution, and optimization of product movement from suppliers to manufacturers and ultimately to customers.
Advanced Transportation Management Systems (TMS): Leverage technology to improve route planning, load optimization, and carrier selection, thus enhancing overall delivery efficiency.
Real-Time Data Utilization: Utilize real-time tracking and data analytics to monitor shipments and make informed decisions that can lead to cost reductions and improved service levels.
Achieving End-to-End Supply Chain Visibility Comprehensive visibility across the supply chain enables manufacturers to monitor the flow of goods at every stage, providing critical insights for proactive decision-making.
Adoption of Modern Technologies: Incorporate technologies such as IoT, RFID, and blockchain to track inventory levels and shipment statuses in real time, thus enhancing transparency and traceability.
Proactive Problem Solving: With enhanced visibility, manufacturers can quickly identify potential disruptions and implement corrective measures before they escalate.

Conclusion
Enhancing supply chain management within manufacturing demands a comprehensive approach that addresses sourcing, logistics, and inventory control. By adopting best practices in these areas, manufacturers can boost operational efficiency, reduce costs, and enhance overall performance.
As the manufacturing industry continues to transform, embracing innovative strategies and technologies will be vital for maintaining a competitive edge. By fostering collaboration and pursuing continuous improvement, manufacturers can build agile and resilient supply chains that meet the challenges of today’s dynamic market.
Through the integration of these practices, manufacturers can achieve greater efficiency, drive significant cost savings, and deliver exceptional value to their customers.
This version presents the information in a new way while retaining the core ideas. Let me know if you need any further adjustments.
#SupplyChainManagement #ManufacturingExcellence #SCM #LogisticsOptimization #InventoryControl #StrategicSourcing #LeanManufacturing #SupplierRelationships #OperationalEffincy #DemandForecasting #SupplyChainOptimization #ManufacturingStrategy #CostReduction #SustainableSupplyChain #ProcessImprovement #SupplyChainSolution #ManufacturingInnovation #WarehouseManagement #RiskManagement #JustInTime #GlobalSupplyChain #DigitalSupplyChain #InventoryManagement #SupplierDiversity #ContinuousImprovement
コメント