Sustainable Manufacturing: Balancing Profitability with Environmental Responsibility
- hr30522
- Oct 9, 2024
- 8 min read
Updated: Nov 20, 2024
In today’s world, where environmental concerns and economic efficiency are increasingly intertwined, the concept of sustainable manufacturing is gaining traction. As industries seek to reconcile their pursuit of profitability with the imperative to reduce their environmental footprint, sustainable manufacturing emerges as a critical strategy. This blog delves into the strategies for making manufacturing processes more sustainable, focusing on energy efficiency, waste reduction, and circular economy practices.
Understanding Sustainable Manufacturing
Sustainable Manufacturing refers to the creation of products through processes that are environmentally responsible and resource-efficient throughout their life cycle. It encompasses practices that minimize waste, reduce energy consumption, and ensure the responsible use of resources. The goal is to balance profitability with environmental responsibility, creating value while reducing the negative impact on the planet.

1. Implementing Energy Management Systems
Energy Management Systems (EMS) help manufacturers monitor and manage energy use more effectively. These systems collect data on energy consumption, identify areas of inefficiency, and suggest improvements. Key components include.
Real-Time Monitoring: EMS provides real-time data on energy use across various processes and equipment. This visibility allows manufacturers to pinpoint inefficiencies and implement corrective actions.
Energy Audits: Regular energy audits help identify opportunities for improvement. By assessing how energy is used, manufacturers can uncover areas where energy-saving measures can be applied.
Performance Metrics: Tracking performance metrics such as energy consumption per unit of production helps in setting benchmarks and goals for energy reduction.
2. Adopting Energy-Efficient Equipment
Investing in energy-efficient equipment can lead to significant reductions in energy consumption. This includes:
High-Efficiency Motors: Upgrading to high-efficiency motors can reduce energy use by 10-30% compared to standard motors.
LED Lighting: Replacing traditional lighting with LED technology decreases energy consumption and extends the lifespan of lighting fixtures.
Advanced HVAC Systems: Modern heating, ventilation, and air conditioning (HVAC) systems are designed to be more energy-efficient, contributing to lower overall energy use.
3. Utilizing Renewable Energy Sources
Incorporating renewable energy sources into manufacturing operations is another way to enhance energy efficiency. Options include:
Solar Power: Installing solar panels can generate clean energy for manufacturing facilities, reducing reliance on non-renewable energy sources.
Wind Power: Wind turbines can provide a substantial amount of energy, particularly in areas with consistent wind patterns.
Biomass Energy: Using biomass from organic materials can offer a renewable alternative to traditional energy sources.

Waste Reduction in Manufacturing
Waste Reduction is a key element of sustainable manufacturing. Minimizing waste not only reduces environmental impact but also lowers production costs. Here are strategies to effectively reduce waste:
1. Lean Manufacturing Techniques
Lean Manufacturing focuses on eliminating waste and improving efficiency. Key lean techniques include:
Value Stream Mapping: Identifying all the steps in the production process and eliminating those that do not add value. This helps in streamlining processes and reducing waste.
Just-In-Time Production: Producing goods only as they are needed, reducing excess inventory and waste.
Kaizen (Continuous Improvement): Encouraging small, incremental changes that improve processes and reduce waste over time.
2. Implementing Waste Segregation and Recycling
Effective waste segregation and recycling practices help in managing and reducing waste. Strategies include:
Segregation: Separating different types of waste (e.g., metals, plastics, paper) at the source to facilitate recycling and proper disposal.
Recycling Programs: Implementing recycling programs for materials such as scrap metal, plastic, and paper can reduce the amount of waste sent to landfills.
Closed-Loop Systems: Establishing closed-loop systems where waste materials are reused within the manufacturing process or repurposed for other uses.
3. Reducing Material Waste
Material Waste Reduction involves optimizing the use of raw materials and minimizing scrap. Techniques include:
Precision Manufacturing: Utilizing advanced technologies such as computer numerical control (CNC) machines to produce components with minimal material waste.
Material Substitution: Choosing alternative materials that are more sustainable or produce less waste during manufacturing.
Process Optimization: Continuously improving production processes to reduce waste and increase yield.
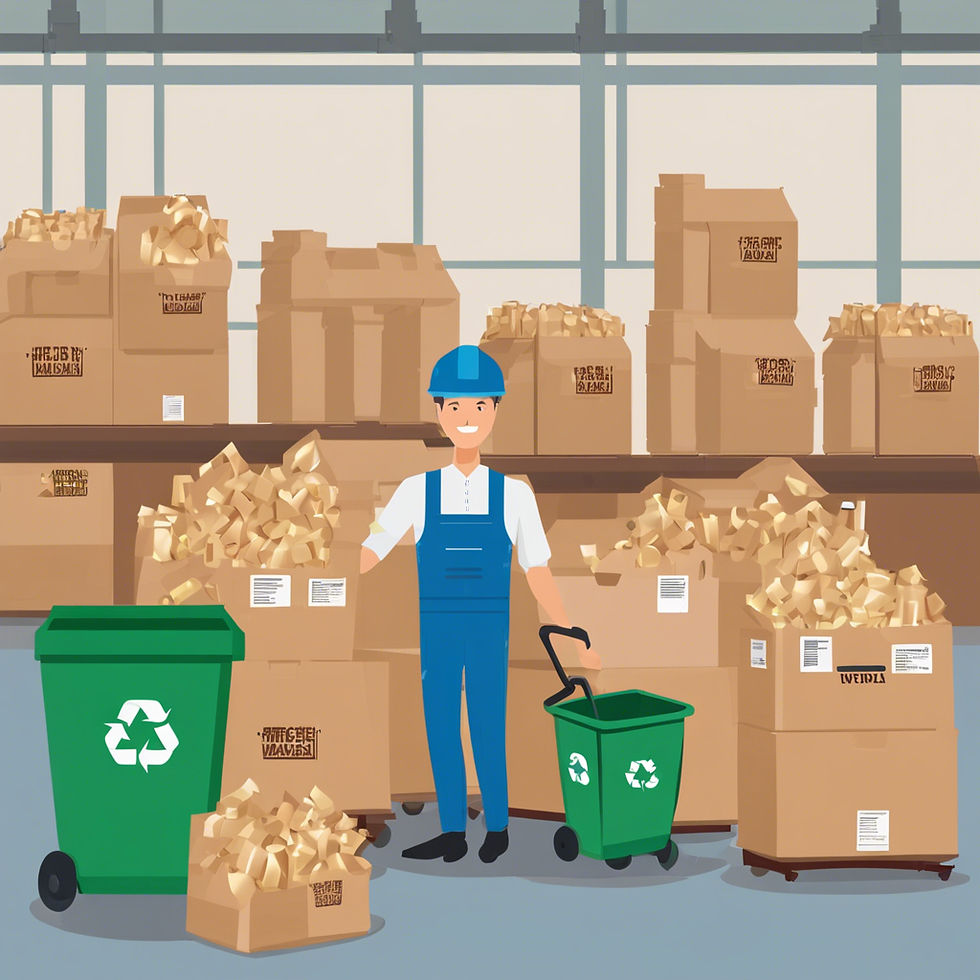
Embracing Circular Economy Practices
The Circular Economy is a model that emphasizes the continuous use of resources by creating closed-loop systems. Unlike the traditional linear model, which follows a "take-make-dispose" approach, the circular economy focuses on:
1. Product Lifecycle Management
Product Lifecycle Management (PLM) involves managing the entire lifecycle of a product from design to disposal. Strategies include:
Design for Disassembly: Designing products so that they can be easily disassembled and their components reused or recycled.
Durability and Repairability: Creating products that are durable and can be repaired or refurbished, extending their lifespan and reducing waste.
Take-Back Programs: Implementing programs to collect and recycle end-of-life products, reducing the environmental impact of product disposal.
2. Resource Recovery and Reuse
Resource Recovery and Reuse focus on reclaiming and reusing materials from end-of-life products. This includes:
Material Recovery: Extracting valuable materials from used products, such as metals and plastics, and reprocessing them for new use.
Industrial Symbiosis: Collaborating with other industries to use by-products or waste materials as inputs for other manufacturing processes.
Circular Supply Chains: Developing supply chains that prioritize the use of recycled or renewable materials, reducing the need for virgin resources.
3. Closed-Loop Production Systems
Closed-Loop Production Systems aim to keep resources in use for as long as possible. Key practices include:
Reverse Logistics: Managing the return of products or materials from consumers to manufacturers for reuse or recycling.
Zero Waste Manufacturing: Striving to achieve zero waste by reusing all materials and minimizing waste generation in production processes.
Eco-Design: Designing products with the end-of-life phase in mind, ensuring that they can be easily recycled or repurposed.
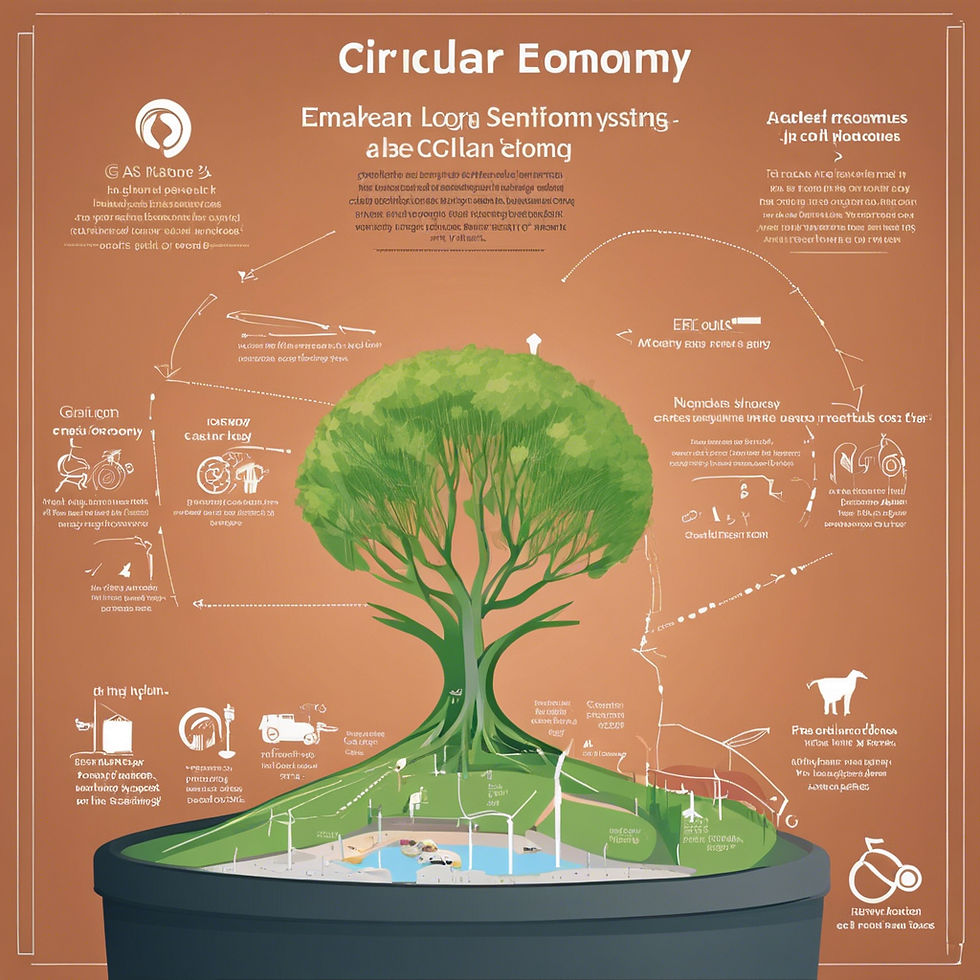
Balancing Profitability with Environmental Responsibility
Striking a balance between profitability and environmental responsibility is crucial for sustainable manufacturing. Manufacturers can achieve this balance by:
1. Integrating Sustainability into Business Strategy
Incorporating sustainability into the core business strategy helps align environmental goals with financial objectives. This includes:
Setting Sustainability Goals: Establishing clear, measurable sustainability goals that drive improvements in energy efficiency, waste reduction, and resource management.
Investing in Sustainable Technologies: Allocating resources to research and development of sustainable technologies that enhance efficiency and reduce environmental impact.
Measuring and Reporting: Tracking and reporting sustainability performance to stakeholders, demonstrating commitment to environmental responsibility and transparency.
2. Engaging Stakeholders
Engaging stakeholders, including employees, customers, and suppliers, is vital for achieving sustainability goals. Strategies include:
Employee Training: Providing training on sustainable practices and encouraging employee involvement in sustainability initiatives.
Customer Education: Educating customers about the environmental benefits of sustainable products and practices.
Supplier Collaboration: Working with suppliers to ensure they adhere to sustainability standards and practices, promoting a more sustainable supply chain.
3. Leveraging Innovation
Innovation plays a key role in balancing profitability with environmental responsibility. Manufacturers can leverage innovation by:
Adopting New Technologies: Embracing emerging technologies that enhance efficiency and reduce environmental impact, such as advanced manufacturing processes and renewable energy solutions.
Exploring New Business Models: Experimenting with business models that promote sustainability, such as product-as-a-service or subscription-based models that reduce waste and encourage recycling.
Continuous Improvement: Committing to continuous improvement in sustainability practices, regularly assessing and refining processes to achieve better environmental and economic outcomes.
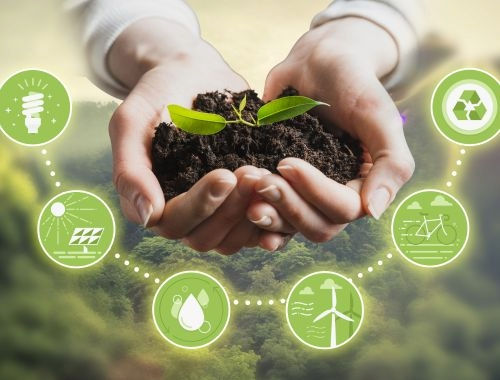
Enhancing Energy Efficiency
Energy Efficiency is a critical component of sustainable manufacturing. Efficient energy use not only reduces costs but also lowers greenhouse gas emissions, contributing to a smaller carbon footprint. Here’s how manufacturers can enhance energy efficiency across their operations:
1. Implementing Energy Management Systems (EMS)
Energy Management Systems (EMS) are designed to monitor, control, and optimize energy use in manufacturing processes. An effective EMS offers several benefits:
Real-Time Monitoring and Analysis: EMS provides continuous monitoring of energy consumption across various machinery and production processes. Real-time data helps identify patterns, inefficiencies, and areas for improvement. For instance, if energy usage spikes unexpectedly, EMS can alert managers to investigate and rectify the issue promptly.
Energy Audits and Assessments: Regular energy audits are integral to understanding energy use and identifying opportunities for improvement. Audits involve a detailed analysis of energy consumption, which can reveal potential savings from upgrading equipment, improving insulation, or altering operational practices.
Performance Benchmarking: By establishing benchmarks for energy consumption, manufacturers can set targets for improvement. Performance metrics such as energy use per unit of production or energy intensity can help track progress and drive continuous improvement.
2. Investing in Energy-Efficient Equipment
Energy-Efficient Equipment plays a vital role in reducing energy consumption and operational costs. Upgrading to more efficient technologies can yield significant savings. Key areas for investment include:
High-Efficiency Motors and Drives: Modern high-efficiency motors and variable frequency drives (VFDs) consume less energy than older models. Upgrading these components can reduce energy use by up to 30%, depending on the application.
Advanced Lighting Solutions: Replacing traditional lighting with LED technology not only reduces energy consumption but also improves lighting quality and longevity. LEDs use up to 80% less energy than incandescent bulbs and have a longer lifespan, reducing maintenance costs.
Efficient HVAC Systems: Upgrading to high-efficiency heating, ventilation, and air conditioning (HVAC) systems can significantly cut energy costs. Advanced HVAC systems include features such as variable speed fans, smart thermostats, and improved insulation, all contributing to reduced energy consumption.
3. Harnessing Renewable Energy Sources
Incorporating Renewable Energy Sources into manufacturing operations reduces dependence on fossil fuels and decreases greenhouse gas emissions. Options for renewable energy include:
Solar Power: Solar panels can be installed on facility rooftops or on nearby land to generate electricity. Solar energy is a clean, renewable resource that can power manufacturing operations and reduce energy costs.
Wind Power: Wind turbines can harness the power of wind to generate electricity. Wind power is particularly effective in regions with consistent wind patterns, providing a reliable source of clean energy.
Biomass Energy: Biomass energy involves using organic materials such as wood, agricultural residues, or industrial by-products to generate heat or electricity. Biomass energy is renewable and can reduce reliance on non-renewable energy sources.

Effective waste management not only minimizes environmental impact but also reduces costs associated with raw materials and waste disposal. Strategies for reducing waste include:
1. Adopting Lean Manufacturing Techniques
Lean Manufacturing focuses on maximizing value while minimizing waste. Key lean techniques include:
Value Stream Mapping: This technique involves mapping out all steps in the production process to identify and eliminate non-value-adding activities. By streamlining processes and removing inefficiencies, manufacturers can reduce waste and improve overall productivity.
Just-In-Time (JIT) Production: JIT production aims to produce goods only as they are needed, minimizing excess inventory and reducing waste. This approach ensures that resources are used efficiently and that inventory levels are aligned with demand.
Kaizen (Continuous Improvement): Kaizen involves making small, incremental changes to improve processes and reduce waste. This continuous improvement approach encourages employees to identify and address inefficiencies regularly, fostering a culture of ongoing enhancement.
2. Implementing Waste Segregation and Recycling
Effective Waste Segregation and Recycling practices help manage waste and promote recycling. Strategies include:
Source Separation: Separating waste materials at the source facilitates easier recycling and disposal. Different types of waste, such as metals, plastics, and paper, should be sorted to maximize recycling efficiency.
Recycling Programs: Implementing recycling programs for materials such as scrap metal, plastic, and paper reduces the amount of waste sent to landfills. By partnering with recycling facilities, manufacturers can ensure that waste materials are processed and reused.
Closed-Loop Systems: Closed-loop systems involve reusing waste materials within the manufacturing process or repurposing them for other applications. For example, recycled plastic can be used to produce new products, reducing the need for virgin materials.
Precision Manufacturing: Advanced manufacturing technologies, such as computer numerical control (CNC) machines, enable precise cutting and shaping of materials. This precision reduces material waste and improves product quality.
Material Substitution: Choosing alternative materials that are more sustainable or produce less waste during manufacturing can significantly impact waste reduction. For example, using recycled materials or bio-based plastics can lower environmental impact.
Process Optimization:
Conclusion
Sustainable manufacturing is not just a trend but a necessity for modern industries aiming to balance profitability with environmental responsibility. By focusing on energy efficiency, waste reduction, and circular economy practices, manufacturers can enhance their operations while minimizing their environmental footprint.
Implementing strategies such as energy management systems, lean manufacturing techniques, and circular economy practices helps manufacturers achieve sustainability goals and drive operational excellence. Balancing environmental responsibility with profitability requires a comprehensive approach that integrates sustainability into business strategy, engages stakeholders, and leverages innovation.
In the end, sustainable manufacturing is about creating a future where economic growth and environmental stewardship go hand in hand. By adopting sustainable practices, manufacturers can not only improve their bottom line but also contribute to a healthier planet and a more sustainable future for generations to come.
#SustainableManufacturing #EcoFriendlyProduction #GreenBusiness #ProfitWithPurpose #CircularEconomy #EcoInnovation #ResponsibleManufacturing #SustainabilityInBusiness #CleanTech #ManufacturingForFuture #ReduceWaste #EnvironmentalImpact #SustainableGrowth #EthicalProduction #GreenEconomy #SustainableDevelopment #EcoConscious#GreenManufacturing #SocialResponsibility #ResourceEfficiency #ZeroWaste #GreenSupplyChain #ClimateAction #SustainableIndustry #EcoEfficiency #RenewableResources #EnvironmentalSustainability #ResponsibleInvesting #InnovationForSustainability #FutureOfManufacturing
Comentarios