The Role of Data Analytics in Manufacturing: Enhancing Decision-Making, Predicting Maintenance Needs, and Optimizing Production Processes
- hr30522
- Oct 9, 2024
- 9 min read
Updated: Nov 20, 2024
In the modern manufacturing landscape, data analytics has emerged as a game-changer. The ability to harness data-driven insights to improve decision-making, predict maintenance needs, and optimize production processes is transforming how manufacturers operate. As the industry moves towards greater efficiency and innovation, leveraging data analytics has become not just beneficial but essential. In this blog, we will explore how data analytics is revolutionizing manufacturing and driving significant improvements across various facets of operations.
The Power of Data Analytics in Manufacturing:
Data Analytics involves the process of examining large datasets to uncover hidden patterns, correlations, and insights that can inform decision-making. For manufacturers, this means transforming raw data from various sources—such as production lines, supply chains, and maintenance logs—into actionable insights that enhance operational efficiency.
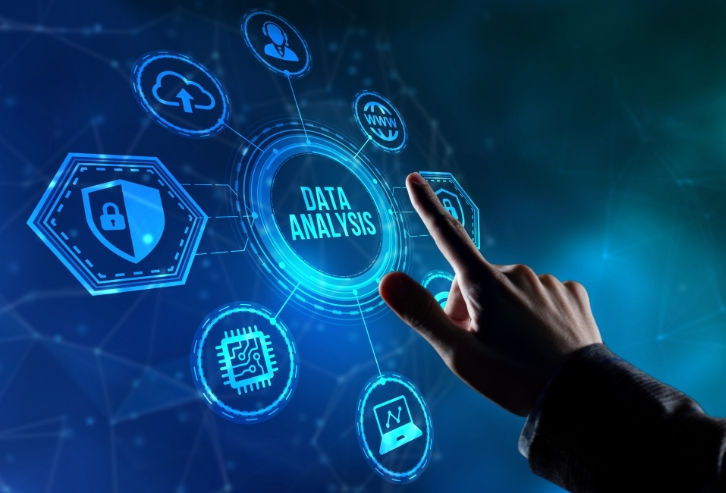
Enhancing Decision-Making
In the fast-paced world of manufacturing, effective decision-making is critical. Data analytics provides manufacturers with the tools to make informed decisions based on empirical evidence rather than intuition or guesswork. Here’s how:
1. Data-Driven Insights:
Data-Driven Insights are the cornerstone of informed decision-making. By analyzing historical and real-time data, manufacturers can gain a clearer understanding of their operations, customer demands, and market trends. For example:
Performance Metrics: Analyzing metrics such as production output, defect rates, and cycle times allows manufacturers to identify bottlenecks and areas for improvement. This information can guide strategic decisions, such as process adjustments or equipment upgrades.
Market Trends: By examining sales data and customer preferences, manufacturers can adjust production plans to align with current market demands. This helps in reducing excess inventory and ensuring that products meet customer expectations.
2. Real-Time Data Analysis:
Real-Time Data Analysis enables manufacturers to make timely decisions that can significantly impact operational efficiency. Advanced analytics tools process data as it is generated, providing up-to-date information that supports:
Quick Responses: In case of unexpected disruptions or deviations from production targets, real-time analytics allows manufacturers to react swiftly and make adjustments to minimize downtime and losses.
Informed Scheduling: Real-time data on machine performance and production rates helps in optimizing scheduling, ensuring that resources are allocated efficiently and production goals are met.
Predicting Maintenance Needs
Maintenance is a critical aspect of manufacturing operations. Unplanned downtime due to equipment failures can result in significant losses. Predictive Maintenance an application of data analytics
helps in mitigating these risks by forecasting maintenance needs before issues arise.
1. Predictive Modeling:
Predictive Modeling involves using historical data and machine learning algorithms to anticipate future equipment failures or maintenance requirements. By analyzing patterns in equipment performance data, manufacturers can:
Forecast Failures: Identify signs of wear and tear or potential failures before they occur. For example, if a particular machine exhibits irregular vibrations or temperature fluctuations, predictive models can signal the need for maintenance.
Optimize Maintenance Schedules: Schedule maintenance activities during planned downtimes or non-peak hours, reducing the impact on production. This proactive approach helps in maintaining equipment in optimal condition and minimizing unexpected breakdowns.
2. Anomaly Detection:
Anomaly Detection is a key component of predictive maintenance. By continuously monitoring equipment data, manufacturers can detect deviations from normal operating conditions. This includes:
Real-Time Alerts: Generating alerts when anomalies are detected, such as unusual noise levels or performance drops. Early detection allows for timely intervention, preventing more severe issues.
Root Cause Analysis: Analyzing anomalies to determine their root causes. This helps in addressing underlying problems and preventing similar issues in the future.

Optimizing Production Processes
Production Optimization is a critical goal for manufacturers looking to enhance efficiency and reduce costs. Data analytics plays a significant role in achieving this by providing insights into various aspects of production.
1. Process Improvement:
Process Improvement involves using data to refine and enhance production processes. Key areas of focus include:
Efficiency Gains: Analyzing production data to identify inefficiencies, such as machine downtime or slow cycle times. Implementing changes based on these insights can lead to increased productivity and reduced waste.
Quality Control: Utilizing data analytics to monitor and control product quality. For instance, statistical process control (SPC) techniques can track variations in product quality and identify factors contributing to defects.
2. Production Forecasting:
Production Forecasting relies on data analytics to predict future production needs based on historical data and market trends. This helps manufacturers:
Align Production with Demand: Forecasting helps in aligning production schedules with expected demand, reducing overproduction and stockouts. Accurate forecasts ensure that manufacturing resources are utilized effectively.
Optimize Inventory Levels: By predicting future production needs, manufacturers can manage inventory levels more efficiently. This reduces carrying costs and minimizes the risk of obsolescence.
3. Process Automation:
Process Automation leverages data analytics to automate repetitive tasks and decision-making processes. Automation tools can:
Streamline Operations: Automate routine tasks such as data entry, report generation, and process monitoring. This frees up valuable human resources for more strategic tasks and enhances overall operational efficiency.
Enhance Accuracy: Reduce human errors in data handling and decision-making. Automated systems ensure that decisions are based on accurate, real-time data, leading to more reliable outcomes.

1. Invest in Technology:
Investing in advanced analytics tools and technologies is essential for harnessing the power of data. This includes:
Big Data Platforms: Utilize big data platforms that can handle large volumes of data from various sources. These platforms support advanced analytics and real-time processing.
Machine Learning Algorithms: Implement machine learning algorithms for predictive modeling and anomaly detection. These algorithms continuously learn from data, improving their accuracy over time.
2. Develop a Data Strategy:
A clear data strategy is crucial for successful data analytics implementation. This involves:
Data Collection: Ensure that data is collected from relevant sources, such as production lines, equipment sensors, and supply chains. High-quality data is essential for accurate analysis.
Data Integration: Integrate data from different systems and sources to create a unified view. Data integration enables comprehensive analysis and insights across the entire manufacturing process.
Data Security: Implement robust data security measures to protect sensitive information. Ensure compliance with data privacy regulations and safeguard against potential cyber threats.
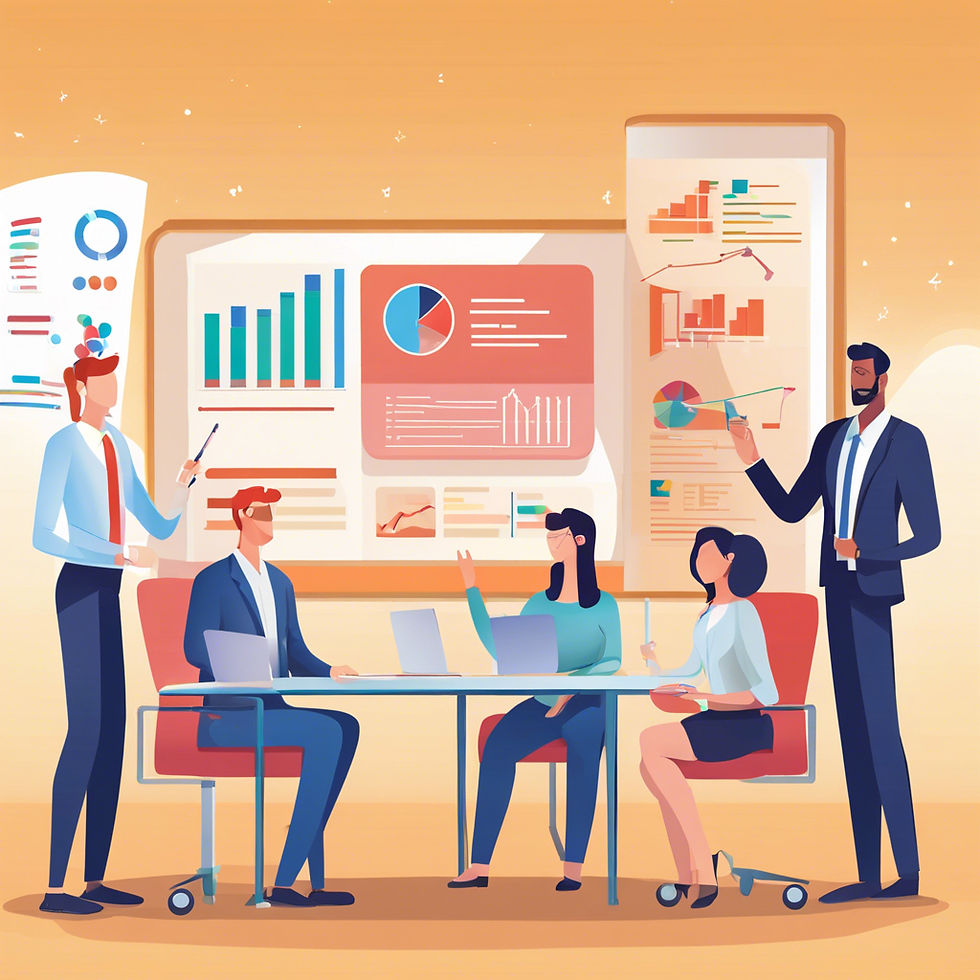
Training and Education: Provide training and education on data analytics tools and techniques. Equip employees with the skills needed to interpret data and make data-driven decisions.
Encourage Collaboration: Foster collaboration between data analysts, engineers, and other stakeholders. Collaborative efforts ensure that insights are effectively applied to improve manufacturing processes.
General Electric (GE) has leveraged data analytics to enhance its manufacturing processes and improve predictive maintenance. By using advanced sensors and analytics, GE can monitor the performance of its jet engines and other machinery in real-time. This approach has allowed GE to predict maintenance needs accurately, reduce downtime, and optimize production efficiency.
Siemens, a global leader in manufacturing and automation, utilizes data analytics to optimize its production processes. By analyzing data from its manufacturing operations, Siemens has been able to identify inefficiencies, improve product quality, and streamline production workflows. This data-driven approach has led to significant cost savings and enhanced operational performance.
the role of data analytics cannot be overstated. The integration of advanced data analytics into manufacturing processes has emerged as a key driver of innovation and efficiency. By leveraging data-driven insights, manufacturers can significantly enhance decision-making, predict maintenance needs with greater accuracy, and optimize production processes. This blog explores how data analytics is transforming manufacturing operations, providing practical insights into how it can be utilized to achieve operational excellence.
Understanding Data Analytics in Manufacturing:
Data Analytics involves the systematic computational analysis of data to uncover patterns, correlations, and insights that inform decision-making. In the context of manufacturing, data analytics encompasses a broad range of activities, including the analysis of production data, equipment performance metrics, supply chain information, and customer feedback. The ultimate goal is to use this data to make informed decisions that enhance operational efficiency and drive business success.
Effective decision-making is a cornerstone of successful manufacturing operations. Data analytics provides manufacturers with the tools to make better decisions based on empirical evidence rather than intuition alone. Here’s how data analytics can enhance decision-making in manufacturing
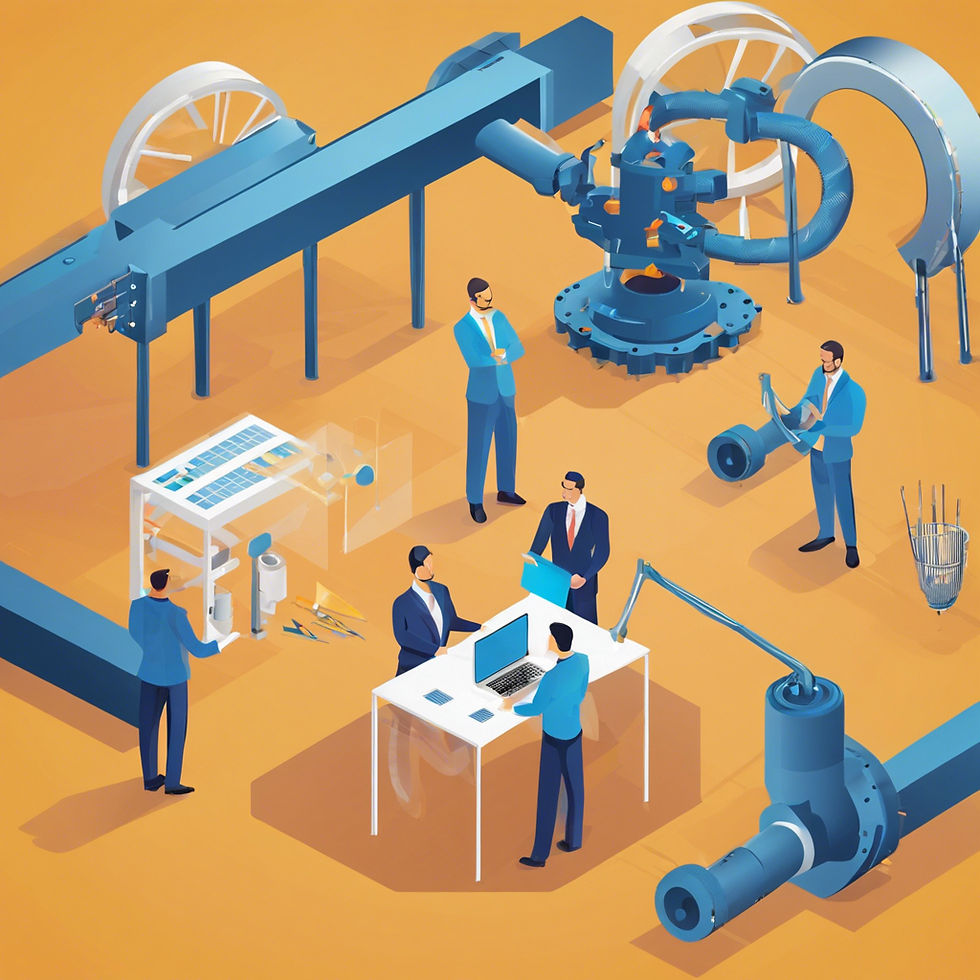
1. Leveraging Data-Driven Insights:
Data-Driven Insights are essential for making informed decisions that drive operational improvements. By analyzing large volumes of data from various sources, manufacturers can gain valuable insights into their operations. Key areas where data-driven insights can be applied include:
Performance Metrics: Data analytics allows manufacturers to track and analyze key performance indicators (KPIs) such as production output, defect rates, and machine utilization. By monitoring these metrics, manufacturers can identify inefficiencies and areas for improvement. For example, if data shows that a particular machine has a higher defect rate, management can investigate the root cause and implement corrective actions.
Market Trends: Analyzing market trends and customer preferences helps manufacturers align their production plans with current demand. For instance, if data indicates a growing demand for a specific product, manufacturers can adjust their production schedules to meet this demand, reducing the risk of overproduction and stockouts.
Operational Performance: Data analytics provides insights into various aspects of operational performance, such as production speed, resource utilization, and process efficiency. By analyzing this data, manufacturers can identify bottlenecks, streamline processes, and enhance overall productivity.
2. Real-Time Data Analysis:
Real-Time Data Analysis enables manufacturers to make timely decisions based on up-to-date information. This capability is crucial for responding to unexpected events and optimizing operations. Real-time data analysis can be applied in several ways:
Immediate Response: When disruptions or deviations occur, real-time data allows manufacturers to respond quickly. For example, if a machine begins to malfunction, real-time data can trigger alerts, enabling maintenance teams to address the issue before it leads to significant downtime.
Dynamic Scheduling: Real-time data on production progress and machine performance allows manufacturers to adjust schedules dynamically. This flexibility ensures that resources are allocated efficiently and production targets are met without unnecessary delays.
Improved Accuracy: Real-time data provides a more accurate picture of current conditions compared to historical data alone. This accuracy is essential for making informed decisions and minimizing errors in production planning.
Maintenance is a critical aspect of manufacturing that directly impacts equipment reliability and operational efficiency. Predictive Maintenance, driven by data analytics, helps manufacturers anticipate maintenance needs and prevent unexpected equipment failures. Here’s how predictive maintenance works:
1. Utilizing Predictive Modeling:
Predictive Modeling involves using historical data and machine learning algorithms to forecast future maintenance needs. By analyzing patterns in equipment performance data, manufacturers can:
Forecast Equipment Failures: Predictive models analyze historical data to identify signs of potential equipment failures. For example, if data shows increasing vibrations or temperature fluctuations in a machine, the model can predict when a failure is likely to occur, allowing for proactive maintenance.
Optimize Maintenance Schedules: Based on predictive insights, manufacturers can schedule maintenance activities during planned downtimes or non-peak hours. This approach minimizes disruptions to production and ensures that equipment remains in optimal condition.
Extend Equipment Life: By addressing maintenance needs before they lead to equipment failures, predictive maintenance helps extend the life of machinery and reduce the frequency of costly repairs or replacements.

Generate Real-Time Alerts: Automated systems can detect anomalies in real-time, such as unusual noise levels or performance drops. Early alerts enable maintenance teams to investigate and address issues before they escalate into major problems.
Conduct Root Cause Analysis: Anomalies often indicate underlying issues that need to be addressed. By analyzing the root causes of anomalies, manufacturers can implement corrective measures to prevent recurrence and improve equipment reliability.
Enhance Operational Reliability: Anomaly detection enhances overall operational reliability by ensuring that potential issues are identified and resolved promptly, reducing the risk of unplanned downtime and production interruptions.
Integrating Data Analytics into Manufacturing Operations:
Successfully integrating data analytics into manufacturing operations requires a strategic approach and the right technology. Here’s how manufacturers can effectively implement data analytics:
1. Invest in Advanced Technology:
Investing in advanced analytics tools and technologies is essential for harnessing the full potential of data. Key technologies include:
Big Data Platforms: Big data platforms handle large volumes of data from various sources and support advanced analytics. These platforms enable manufacturers to analyze and process data efficiently, providing valuable insights into operations.
Machine Learning Algorithms: Machine learning algorithms are used for predictive modeling, anomaly detection, and process optimization. These algorithms continuously learn from data, improving their accuracy and providing more precise forecasts and predictions.
Data Visualization Tools: Data visualization tools help present complex data in an easily understandable format. Interactive dashboards, charts, and graphs make it easier for stakeholders to interpret data and make informed decisions.
2. Develop a Robust Data Strategy:
A clear and comprehensive data strategy is crucial for effective data analytics implementation. Key components of a data strategy include:
Data Collection: Ensure that data is collected from relevant sources, such as production lines, equipment sensors, and supply chains. High-quality data is essential for accurate analysis and decision-making.
Data Integration: Integrate data from different systems and sources to create a unified view. Data integration enables comprehensive analysis and insights across the entire manufacturing process.
Data Security: Implement robust data security measures to protect sensitive information. Ensure compliance with data privacy regulations and safeguard against potential cyber threats.
Training and Education: Provide training and education on data analytics tools and techniques. Equip employees with the skills needed to interpret data and make data-driven decisions.
Encourage Collaboration: Foster collaboration between data analysts, engineers, and other stakeholders. Collaborative efforts ensure that insights are effectively applied to improve manufacturing processes.
Promote Data Literacy: Promote data literacy across the organization by emphasizing the importance of data-driven decision-making. Encourage employees
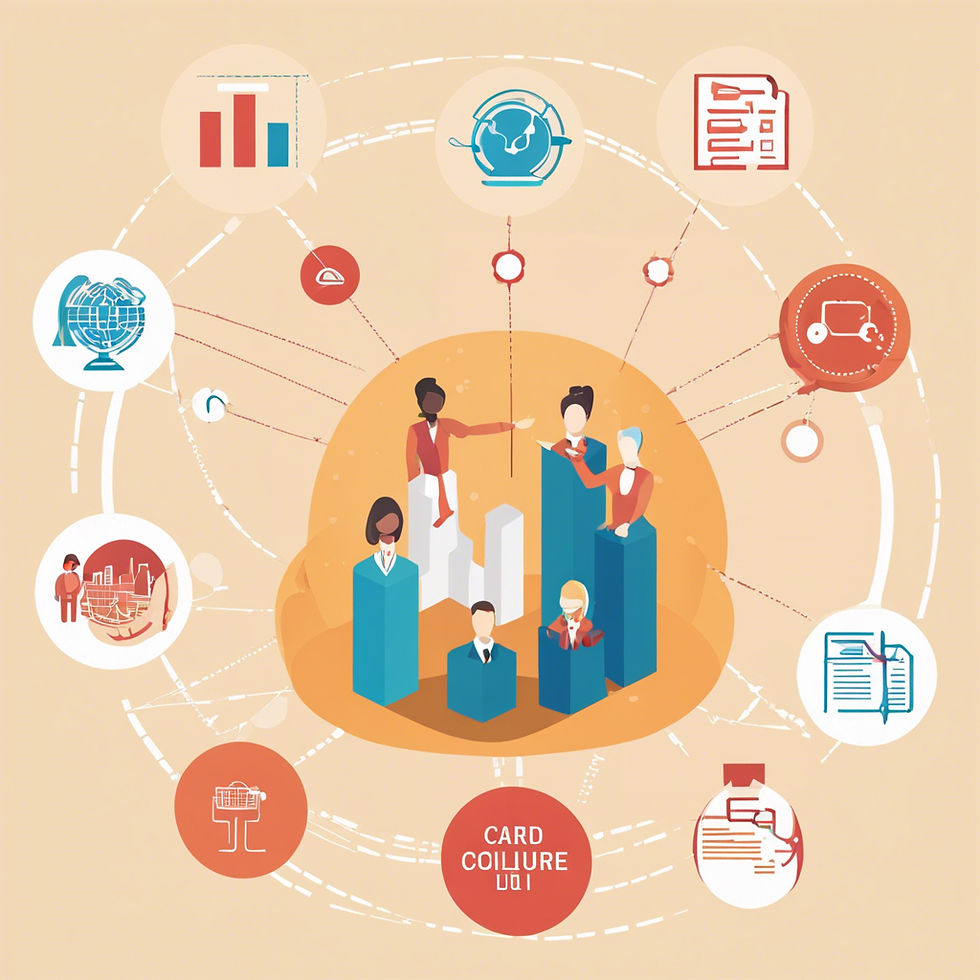
Conclusion
Data analytics is revolutionizing the manufacturing industry by providing valuable insights that enhance decision-making, predict maintenance needs, and optimize production processes. By harnessing the power of data-driven insights, manufacturers can achieve greater efficiency, reduce costs, and drive continuous improvement.
Investing in advanced analytics technologies, developing a robust data strategy, and fostering a data-driven culture are key steps in effectively leveraging data analytics. As the manufacturing landscape continues to evolve, embracing data analytics will be crucial for staying competitive and achieving long-term success.
#DataAnalytics #ManufacturingInnovation #SmartManufacturing #PredictiveMaintenance #DataDrivenDecisions #OperationalExcellence #ManufacturingAnalytics #ProcessOptimization #Industry40 #BigDataInManufacturing #IoTInManufacturing #AnalyticsInIndustry #EfficiencyThroughData #DigitalTransformation #ManufacturingInsights #HarnessingDataForManufacturing #AnalyticsDrivenManufacturing #EnhancingDecisionMakingWithData #PredictiveAnalyticsInManufacturing #OptimizingProductionThroughAnalytics #SmartFactoriesWithDataInsights #DataAnalyticsForManufacturingSuccess #TransformingManufacturingWithData #InnovativeManufacturingSolutions
Comments