The Role of ERP in Regulatory Compliance for Sugar and Ethanol Manufacturers
- hr30522
- Jul 10, 2024
- 8 min read
Updated: Nov 29, 2024
In the modern industrial landscape, the production of sugar and ethanol plays a pivotal role, serving as essential components in various industries and everyday products. However, this vital sector operates within a highly regulated environment, subject to a plethora of industry-specific regulations and standards. From stringent environmental mandates to intricate quality control measures, compliance with these regulations is paramount for sugar and ethanol manufacturers to ensure operational efficiency, product quality, and sustainability.
In this blog post, we delve into the intricate world of regulatory compliance for sugar and ethanol manufacturers, exploring the challenges they face and the pivotal role Enterprise Resource Planning (ERP) systems play in facilitating adherence to industry regulations and standards. We will examine how ERP systems streamline compliance processes, enhance data management, and empower companies to navigate the complex regulatory landscape effectively.
Understanding Regulatory Compliance in the Sugar and Ethanol Industry:
Before delving into the role of ERP systems, it's essential to understand the regulatory landscape in which sugar and ethanol manufacturers operate. The production of sugar and ethanol involves numerous processes, each subject to specific regulations aimed at ensuring environmental sustainability, product safety, and operational transparency.
1. Environmental Regulations:
Sugar and ethanol manufacturing processes can have a significant impact on the environment, from water and air pollution to waste management. Regulatory bodies impose stringent standards to mitigate these impacts, requiring manufacturers to adhere to emission limits, wastewater treatment protocols, and sustainable practices.
2. Quality Standards:
Ensuring product quality and safety is paramount in the sugar and ethanol industry. Regulatory agencies establish quality standards and specifications for sugar and ethanol products, encompassing parameters such as purity, moisture content, and chemical composition.
3. Safety Protocols:
Workplace safety and employee welfare are critical considerations for sugar and ethanol manufacturers. Regulations mandate compliance with occupational health and safety standards to prevent accidents, minimize hazards, and protect workers' well-being.
4. Financial Compliance:
In addition to industry-specific regulations, sugar and ethanol manufacturers must comply with financial regulations governing taxation, financial reporting, and trade practices. Adherence to these regulations ensures transparency, accountability, and financial stability within the industry.
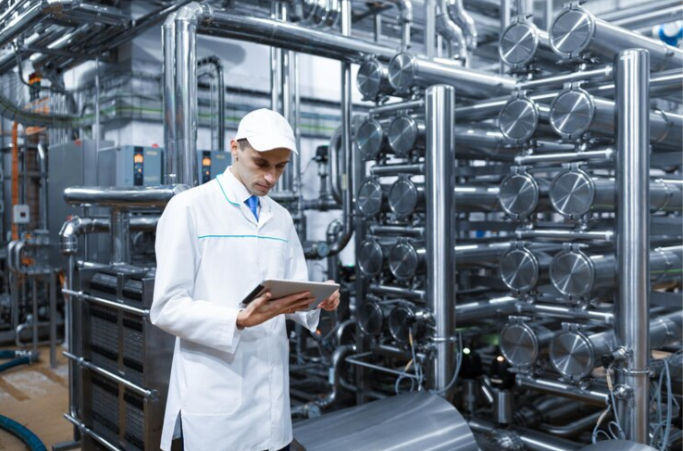
Challenges of Regulatory Compliance for Sugar and Ethanol Manufacturers:
Compliance with industry regulations poses several challenges for sugar and ethanol manufacturers, stemming from the complexity of regulatory requirements and the dynamic nature of the regulatory landscape.
1. Complexity:
The regulatory framework governing the sugar and ethanol industry is multifaceted, encompassing a diverse range of regulations, standards, and guidelines. Navigating this complexity requires a deep understanding of regulatory requirements and the ability to interpret and implement them effectively.
2. Data Management:
Compliance with industry regulations necessitates the collection, management, and analysis of vast amounts of data, including production metrics, environmental monitoring data, and quality control records. Managing this data efficiently and accurately is a daunting task, particularly in the absence of centralized systems and standardized processes.
3. Integration Issues:
Sugar and ethanol manufacturers often rely on disparate systems and manual processes to manage various aspects of their operations, including production, inventory management, and regulatory compliance. The lack of integration between these systems hinders data visibility, coordination, and compliance management, leading to inefficiencies and compliance risks.
4. Risk of Non-compliance:
Non-compliance with industry regulations carries significant consequences for sugar and ethanol manufacturers, including fines, penalties, legal liabilities, and reputational damage. The dynamic nature of regulations and the potential for regulatory changes further amplify the risk of non-compliance, necessitating proactive measures to stay abreast of regulatory developments.
How ERP Systems Help:
An ERP system can help sugar and ethanol manufacturers overcome these challenges by providing a centralized platform for data management, tracking, and reporting. Some key features of ERP systems that support regulatory compliance include:
1.Inventory Management: ERP systems can track and report on inventory levels, ensuring accurate record-keeping and compliance with regulatory requirements.
2.Batch Tracking: ERP systems can automate batch tracking and reporting, ensuring that production batches are accurately recorded and tracked.
3.Quality Control: ERP systems can automate quality control checks, ensuring that products meet regulatory standards.
4.Automated Reporting: ERP systems can generate automated reports, ensuring that compliance requirements are met.
5.Data Integration: ERP systems can integrate data from multiple sources, providing a single source of truth for regulatory compliance.

The Role of ERP Systems in Regulatory Compliance:
Enterprise Resource Planning (ERP) systems have emerged as indispensable tools for sugar and ethanol manufacturers seeking to streamline compliance processes, enhance data management, and mitigate compliance risks. ERP systems offer comprehensive functionalities tailored to the specific needs of the sugar and ethanol industry, enabling manufacturers to navigate the complex regulatory landscape effectively. Let's explore the key ways in which ERP systems facilitate regulatory compliance for sugar and ethanol manufacturers.
1. Centralized Data Management:
One of the primary benefits of ERP systems is their ability to centralize data from various departments and processes within an organization. By consolidating data related to production, inventory management, quality control, and regulatory compliance into a single integrated platform, ERP systems provide manufacturers with a unified view of their operations. This centralized approach streamlines data management, improves data accuracy and consistency, and enhances compliance reporting capabilities.
2. Real-time Monitoring and Reporting:
ERP systems enable sugar and ethanol manufacturers to monitor key performance indicators (KPIs) related to regulatory compliance in real-time. By integrating sensors, IoT devices, and other data sources into the ERP system, manufacturers can capture and analyze operational data continuously, identify compliance deviations or anomalies, and take corrective actions promptly. Moreover, ERP systems offer robust reporting functionalities, allowing manufacturers to generate compliance reports, regulatory filings, and audit documentation accurately and efficiently.
3. Integrated Processes:
ERP systems facilitate the integration of various business processes involved in sugar and ethanol manufacturing, including production planning, procurement, inventory management, quality assurance, and regulatory compliance. By connecting these processes seamlessly within a unified platform, ERP systems ensure data consistency, process transparency, and cross-functional collaboration. This integrated approach enables manufacturers to align their operations with regulatory requirements at every stage of the production cycle, from raw material sourcing to product distribution.
4. Adaptable to Regulatory Changes:
The regulatory landscape governing the sugar and ethanol industry is subject to frequent changes and updates, necessitating adaptability and agility in compliance management. ERP systems are designed to accommodate regulatory changes swiftly, allowing manufacturers to update compliance-related processes, workflows, and reporting requirements in response to new regulations or standards. With configurable workflows, rule-based automation, and flexible reporting capabilities, ERP systems empower manufacturers to stay compliant with evolving regulatory requirements without significant disruptions to their operations.
5. Risk Management:
ERP systems incorporate robust risk management functionalities to help sugar and ethanol manufacturers identify, assess, and mitigate compliance risks proactively. By conducting risk assessments, defining control measures, and monitoring compliance performance indicators, ERP systems enable manufacturers to anticipate potential compliance issues, implement corrective actions, and mitigate risks before they escalate. Moreover, ERP systems facilitate audit trail capabilities, ensuring traceability and accountability in compliance-related activities, such as data entry, approvals, and documentation.
6. Enhanced Efficiency and Cost Savings:
By automating repetitive tasks, streamlining workflows, and eliminating manual errors, ERP systems enhance operational efficiency and reduce compliance-related costs for sugar and ethanol manufacturers. The automation of compliance processes, such as data collection, reporting, and audit preparation, reduces the time and effort required for compliance management, allowing manufacturers to allocate resources more effectively. Moreover, the avoidance of penalties, fines, and other costs associated with non-compliance contributes to significant cost savings and risk mitigation in the long run.
To illustrate the practical impact of ERP systems on regulatory compliance in the sugar and ethanol industry, let's consider a case study of ABC Sugar and Ethanol Company, a leading manufacturer in the sector. ABC Company embarked on an ERP implementation initiative to enhance its compliance management capabilities and address the challenges posed by regulatory complexity and data management.
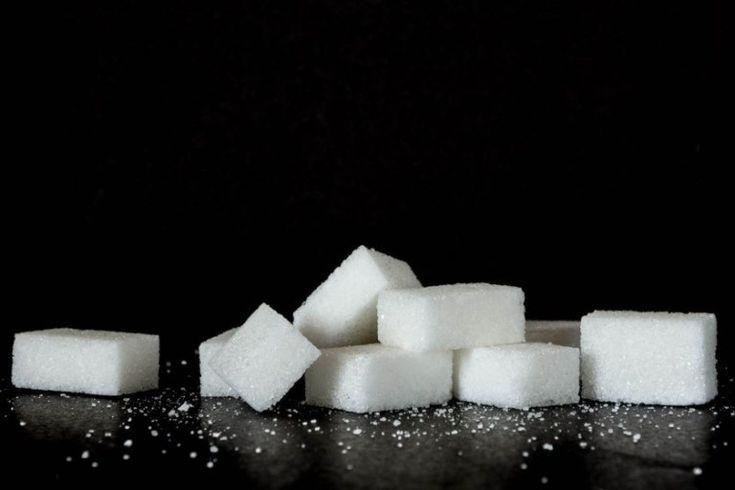
1. Streamlined Compliance Processes:
By implementing an ERP system tailored to its specific needs, ABC Company was able to streamline compliance processes across its operations. The centralized data repository provided by the ERP system enabled ABC Company to consolidate compliance-related data from multiple sources, including production facilities, laboratories, and regulatory agencies. This centralized approach facilitated efficient data collection, analysis, and reporting, reducing the time and effort required for compliance management.
2. Enhanced Visibility and Control:
The real-time monitoring capabilities of the ERP system provided ABC Company with unparalleled visibility into its compliance performance. Dashboards, reports, and alerts enabled stakeholders to track key compliance metrics, identify deviations from regulatory requirements, and take corrective actions promptly. By proactively monitoring compliance indicators, ABC Company was able to maintain control over its operations and mitigate compliance risks effectively.
3. Improved Decision-making:
Access to accurate and up-to-date data facilitated informed decision-making at ABC Company. The ERP system provided executives, managers, and compliance officers with comprehensive insights into compliance performance, regulatory trends, and emerging risks. Armed with this information, ABC Company could make data-driven decisions to optimize its compliance strategies, allocate resources efficiently, and address compliance gaps proactively.
4. Cost Reduction:
The implementation of the ERP system resulted in significant cost savings for ABC Company by automating manual tasks, reducing errors, and minimizing the risk of non-compliance. By streamlining compliance processes, ABC Company was able to allocate resources more effectively, optimize operational workflows, and avoid penalties and fines associated with non-compliance. Moreover, the enhanced efficiency and transparency provided by the ERP system contributed to improved operational performance and profitability for ABC Company.
As a sugar and ethanol manufacturer, regulatory compliance is a crucial aspect of daily operations. With the ever-changing landscape of regulations and standards, it's essential to have a robust Enterprise Resource Planning (ERP) system in place to ensure compliance. An ERP system can help sugar and ethanol manufacturers navigate the complex regulatory requirements by providing a centralized platform for data management, tracking, and reporting.
By integrating all business processes, including production, inventory management, and quality control, an ERP system can help companies maintain accurate records and adhere to industry regulations. For instance, an ERP system can track and report on inventory levels, batch production, and quality control checks to ensure compliance with regulations such as Good Manufacturing Practices (GMP) and Food Safety Modernization Act (FSMA). Additionally, an ERP system can automate workflows and notifications, ensuring that all necessary steps are taken to prevent non-compliance. By implementing an ERP system, sugar and ethanol manufacturers can reduce the risk of non-compliance, improve operational efficiency, and increase customer satisfaction. With an ERP system, companies can have confidence in their ability to meet regulatory requirements, focus on growth and innovation, and ultimately maintain a competitive edge in the market.

Benefits of ERP in Regulatory Compliance:
Implementing an ERP system can bring numerous benefits to sugar and ethanol manufacturers, including:
1.Improved Compliance:
ERP systems can help ensure compliance with regulatory requirements, reducing the risk of non-compliance.
2.Increased Efficiency:
ERP systems can automate many tasks, reducing the time and effort required for compliance activities.
3.Improved Data Accuracy:
ERP systems can provide accurate and up-to-date data, reducing errors and improving decision-making.
4.Reduced Risk:
ERP systems can help reduce the risk of non-compliance, financial penalties, and reputational damage.
Conclusion:
In conclusion, regulatory compliance is a critical challenge for sugar and ethanol manufacturers, given the complexity of industry regulations and the consequences of non-compliance. Enterprise Resource Planning (ERP) systems play a pivotal role in helping manufacturers navigate the regulatory landscape effectively, streamline compliance processes, and mitigate compliance risks. By centralizing data management, enabling real-time monitoring and reporting, integrating processes, adapting to regulatory changes, facilitating risk management, and enhancing efficiency and cost savings, ERP systems empower sugar and ethanol manufacturers to achieve and maintain compliance with industry regulations and standards. As the regulatory landscape continues to evolve, investing in robust ERP solutions will remain imperative for sugar and ethanol manufacturers seeking to ensure operational excellence, product quality, and sustainability in a highly regulated environment.
By providing a centralized platform for data management, tracking, and reporting, an ERP system can help manufacturers navigate the complex regulatory landscape. With an ERP system, sugar and ethanol manufacturers can improve compliance, increase efficiency, improve data accuracy, and reduce risk. By implementing an ERP system, you can ensure that your business is well-equipped to meet the challenges of regulatory compliance.
#RegulatoryCompliance #ERPSystems #SugarIndustry #EthanolProduction#ComplianceManagement
#ERPSoftware #ManufacturingCompliance #RegulatoryStandards #FoodSafetyRegulations #EnvironmentalCompliance #QualityManagement #DataCompliance #ComplianceTracking #IndustryRegulations #SustainableManufacturing #SmartManufacturing #AuditTrail
Comments